Vinhaça: Biodigestão X Incineração
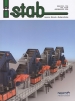
Brasil e Índia são respectivamente o primeiro e o segundo maiores produtores de cana de açúcar.
Enquanto o Brasil é o segundo maior produtor de etanol combustível, a produção de etanol na Índia é ainda incipiente com a tendência de aumentar de forma progressiva já que, do ponto de vista ambiental, provavelmente deve fazer mais sentido subsidiar a produção de etanol no lugar de subsidiar a produção de açúcar, como ocorre hoje em dia.
Os dois países apresentam condições de produção de cana totalmente diferentes em ambientes agronômicos completamente distintos. Desta maneira, as soluções para mitigar os problemas ambientais que podem ser causados pela vinhaça resultante da produção do etanol são também bastante díspares nos dois países.
No Brasil estamos passando gradativamente da aplicação da vinhaça in natura no campo para uma concentração parcial da vinhaça, visando otimizar esta aplicação, e também está sendo proposta em anos recentes a biodigestão da vinhaça para a produção de biogás, visando a geração de energia elétrica ou de calor.
Na Índia estão preconizando a incineração da vinhaça para recuperar até 90% do potássio nas cinzas das caldeiras e para a produção de energia elétrica excedente. Esta posição ficou marcante durante o Congresso da ISSCT do ano passado na Argentina, onde vários fornecedores indianos preconizaram esta solução como sendo a mais indicada do ponto de vista técnico e econômico, pelo menos para as condições vigentes na Índia.
A questão que surge então é se a incineração da vinhaça também poderia ser adotada com sucesso no caso do Brasil. Assim este texto tem por objetivo fazer uma comparação hipotética de uma planta com mix açúcar na faixa de 50%, produzindo cerca de 500 m³/d de etanol anidro combustível e com a perspectiva de exportar todo o excedente energético na forma de energia elétrica, com biodigestão ou com incineração da vinhaça.
Antes de estabelecermos as premissas dos projetos a serem comparados é recomendável uma breve descrição dos dois sistemas envolvidos.
Já escrevemos anteriormente sobre a produção de energia elétrica a partir da biodigestão da vinhaça, e assim sugerimos verificar as informações a respeito contidas nos textos da Revista STAB da edição maio/junho de 2008 (Energia Elétrica a partir da Vinhaça) e da edição maio/junho de 2016 (Produção de Biogás: Lagoa x Reator), ambas disponíveis no nosso site na internet. Embora o biogás produzido possa ser queimado em caldeiras existentes, trata-se de um ciclo termodinâmico de baixa eficiência, e assim vamos usar na nossa comparação a produção de energia elétrica com motores de combustão interna com previsão de um sistema para a desulfurização do biogás.
Na Índia a capacidade média das usinas é bem menor do que no Brasil e lá já existem várias caldeiras queimando vinhaça, pelos relatos a maior delas tem capacidade de 75 t/h, estando as demais na faixa entre 25 t/h e 40 t/h. Estas caldeiras produzem vapor na faixa de 45 bar e 400 ºC com água de alimentação na faixa de 150 ºC, ainda não está disponível por lá uma tecnologia que seja adequada para produzir vapor com temperatura mais alta.
Embora todos os fabricantes indianos mencionem que estão desenvolvendo tecnologia para queimar 100% de vinhaça, hoje em dia o normal é usar uma relação em peso de 80% de vinhaça e de 20% de bagaço como combustível suporte. O bagaço com 50% de umidade e a vinhaça com 60% de brix, a caldeira operando com uma eficiência de 80% a 82% sobre o PCI combinado dos dois combustíveis. O consumo de energia elétrica na caldeira está na faixa de 7,5 a 8,0 kWh/t de vapor. A retenção de particulados deve ser feita a seco para recuperar o máximo de potássio, e a tecnologia com filtro de mangas tem sido a preferida em relação ao precipitador eletrostático, com previsão de substituição das mangas a cada quatro safras. Os fabricantes mencionam recuperação de 99% das cinzas e de 95% do potássio disponível na vinhaça (para referência vide texto Multiciclone x Precipitador da edição março/abril de 2019 da Revista STAB).
O vapor motriz produzido pode acionar um turbo gerador de condensação com uma extração controlada de vapor a uma pressão adequada para promover a concentração da vinhaça. Desta maneira a energia térmica para concentrar a vinhaça é produzida pela incineração da mesma, com produção de energia elétrica excedente e com sobra de condensados com alto teor de VOC (compostos orgânicos voláteis), mas sem potássio.
A má notícia é que a tecnologia adotada da Índia ainda exige limpeza periódica manual com ar comprimido nos feixes tubulares da caldeira que dura uma semana, em função dos depósitos causados pela queima da vinhaça. A informação que obtivemos no Congresso da Argentina é uma garantia dos fabricantes de 90 dias de operação sem limpeza, sendo que na prática chegaram a períodos de 150 dias sem limpeza. Se considerarmos uma média de 120 dias entre limpezas, vamos ter a caldeira parada durante uma semana em uma safra de oito meses, mas de qualquer maneira deverá ser prevista uma estratégia para concentrar vinhaça com bagaço excedente e um reservatório para acumular uma semana de vinhaça com 60% de brix, sendo que por segurança será melhor prever duas paradas e uma sobre capacidade de 15% a 20% no concentrador de vinhaça.
Agora podemos imaginar uma planta produzindo açúcar e etanol anidro com a premissa de exportar energia elétrica, processando 2,4 mmtc a um ritmo de 500 t/h durante 4.800 horas efetivas e com 85% de eficiência de tempo aproveitado, sem palha adicional para simplificar. Vamos considerar a cana com valores médios de 14,7% de ART e de 12,5% de fibra. Vamos também considerar a fermentação produzindo vinho centrifugado com 10% v/v e um volume de vinhaça de 9,0 l/l com 3,5% de brix e 35.000 ppm de DQO. Não vamos considerar a prática indiana de recirculação de vinhaça na fermentação, já que não pretendemos considerar rendimentos fermentativos diferentes neste caso, e não vamos considerar a biodigestão de torta de filtro, pois produções significativas de biogás a partir da torta são indicação de provável perda excessiva de açúcar na mesma.
Para ambas as alternativas Biodigestão (AB) e Incineração (AI) consideramos uma caldeira queimando bagaço e gerando vapor motriz com 68 bar(a) e 525 ºC e consumindo 40% de vapor no processo. Para a AB consideramos os biodigestores e a geração de energia com motores de combustão interna, sem concentração de vinhaça. Para a AI vamos considerar uma segunda caldeira e um turbo gerador com sistema de concentração de vinhaça. Em todos os casos vamos considerar operação apenas durante o período de safra, sem nenhuma geração no período de entressafra.
Os parâmetros comparativos obtidos em nossos estudos estão indicados de forma simplificada na Tabela 1 abaixo.
Parâmetro |
Biodigestão (AB) |
Incineração (AI) |
Geração de energia a partir do bagaço na safra e safrinha (kWh/tc) |
106,9 |
103,9 |
Consumo de energia da usina na safra e safrinha (kWh/tc) |
39,6 |
39,6 |
Excedente de energia exportável da usina (kWh/tc) |
67,3 |
64,3 |
Geração de energia da planta anexa (kWh/tc) |
12,8 |
7,4 |
Consumo de energia da planta anexa (kWh/tc) |
0,6 |
0,8 |
Excedente de energia exportável da planta anexa (kWh/tc) |
12,2 |
7,4 |
Excedente de energia exportável total (kWh/tc) |
79,5 |
70,9 |
Capex da planta da planta anexa (estimativa em R$ milhões) |
80 (*) |
70 (**) |
Opex da planta anexa (estimativa em R$/tc) |
1,32 |
2,93 |
Aplicação do potássio recuperado na lavoura |
via úmida diluída |
via seca |
Opex para aplicação de potássio na lavoura (estimativa em R$/tc) |
(***) |
(***) |
(*) Biodigestores 63%, moto-geradores 37%
(**) Caldeira e turbo gerador 56%, concentrador de vinhaça 44%
(***) Valores que dependem das condições agronômicas específicas de cada planta.
Os resultados acima devem ser interpretados considerando-se uma série de particularidades de cada uma das alternativas estudadas.
Não consideramos na comparação a utilização de sistemas integrados de destilação com concentração, já que existem inúmeras opções técnicas possíveis, e este seria um estudo específico caso a caso. Sistemas integrados tendem a favorecer mais a AI, já que na AB haveria uma menor eficiência térmica global em função da necessidade de resfriamento da vinhaça antes do biodigestor e posterior aquecimento da mesma antes da concentração.
Conforme mencionado acima, não consideramos neste estudo a recirculação de vinhaça na fermentação, que é prática usual na Índia, com uma recirculação na faixa de 30% a 35% e produção de vinhaça na faixa de 5,5 l/l a 6,0 l/l com 12% a 14% de sólidos. A recirculação de vinhaça tem como consequência uma redução significativa no gasto de vapor para a sua concentração, já que a água a ser evaporada diminui cerca de 50% e assim o investimento no concentrador de vinhaça é muito menor. Em compensação, o teor de cinzas da vinhaça indiana é muito mais alto do que no Brasil, porque além da recirculação da vinhaça o mel final é muito esgotado. Em consequência o poder calorífico (PCI) da vinhaça concentrada no Brasil tenderia a ser mais alto na faixa de 10% a 15%, mas é impossível garantir, pois como na Índia em geral há uma menor recuperação de leveduras, os sólidos totais lá podem significar um PCI mais elevado.
O que é indispensável é começarmos a fazer no Brasil uma adequada caracterização da nossa vinhaça, para levar em conta além do brix também os sólidos em suspensão. Esta caracterização adequada vai poder definir com mais segurança a real quantidade de energia que poderia ser recuperada da vinhaça.
Do ponto de vista de redução de investimento e de aumento de exportação de energia concluímos que a recirculação da vinhaça na fermentação ajuda muito a viabilizar a AI na Índia. Simulando a AI com recirculação de vinhaça teríamos uma exportação de energia de 84,3 kWh/tc (no lugar de 70,9 kWh/tc da tabela acima, ou seja, aproximadamente ganha em vez de perder 5,0 kWh/tc em relação à AB) e uma redução no Capex da planta anexa ao redor de R$ 14 milhões. Fica o dilema para os especialistas em fermentação, definir qual seria a perda na produção de etanol em função de uma provável menor eficiência fermentativa decorrente da recirculação da vinhaça.
Resta agora discutir os fatores de comparação intangíveis cuja precificação é mais difícil determinar.
A AB trabalha com uma biomassa viva sob forma de lodo granulado. Como na fermentação alcoólica há necessidade de cuidados especiais para manter estável a operação de biodigestão. Uma eventual perda de lodo requer um período elevado para estabilização operacional. A AI utiliza apenas princípios físico-químicos, mais previsíveis, porém ainda necessita de limpeza manual periódica com os riscos daí decorrentes.
A vinhaça a ser aplicada no campo na AB ainda deve respeitar as limitações ambientais em função do potássio presente na mesma. Na AI os condensados resultantes podem ser aplicados em áreas próximas com custos muito menores, e o potássio recuperado com as cinzas da caldeira pode ser aplicado como um fertilizante mineral. Fica o dilema para os agrônomos especialistas em aplicação de vinhaça, definir qual seria a diferença de Opex entre a AB e a AI.
Assim a conclusão preliminar deste estudo é que a AI pode ser praticada na Índia em função da alta reciculação de vinhaça no sistema de fermentação, necessitando de menos energia na concentração e produzindo uma vinhaça que, embora com alta teor de cinzas, pode ter um PCI mais elevado notadamente devido a um maior teor de sólidos em suspensão, decorrente da baixa recuperação de levedura ou eventual operação com levedura perdida.
Vamos agora na próxima oportunidade fazer uma comparação entre a AB e uma AI adotando, no lugar da tecnologia indiana, uma tecnologia já disponível no Brasil, que permite queimar a vinhaça com um menor nível de concentração em caldeiras com leito fluidizado.
Mas é importante voltar a ressaltar que em qualquer caso fica patente a urgente necessidade de caracterizarmos com critério o PCI da vinhaça, já que muito mais importante do que o valor do brix é definir também o teor e as características dos sólidos em suspensão.