Recuperação de sacarose na cristalização e centrifugação
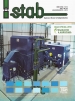
Estivemos trabalhando recentemente no projeto básico de uma usina no exterior cuja finalidade era aumentar a recuperação de açúcar e reduzir a produção de etanol, cujo sistema de fermentação opera somente com melaço esgotado. A usina opera com sistema de três massas cozidas e possui uma refinaria anexa.
Embora operando com três massas, a pureza do mel final estava muito elevada, mesmo levando-se em conta o retorno do mel esgotado da refinaria que sempre impacta na recuperação final. O corpo técnico da usina já estava com uma solução pronta que fora indicada por fabricantes de equipamentos. Bastava instalar um tacho contínuo na massa C e cristalizadores verticais para baixar a pureza do mel final e assim aumentar a recuperação.
Entretanto, analisando mais de perto os problemas, pudemos constatar que o tacho de massa C não deveria nem de longe ser considerado como uma prioridade para os investimentos.
Investir na fase final do processo sem corrigir etapas anteriores costuma ser dinheiro mal empregado. É mais ou menos como dar a máxima atenção ao sexto terno da moenda quando o primeiro está operando muito mal. Não faz sentido.
A nossa intenção no texto de hoje é discutir alguns aspectos básicos e inequívocos dos sistemas de cristalização e de centrifugação existentes nas usinas de cana.
É fato que sistemas que combinam múltiplas etapas de cristalização da sacarose são sistemas de implicam recirculação de produtos intermediários. Eles são por natureza sistemas interativos. Em outras palavras, isto significa que para chegar a um equilíbrio do processo tais sistemas necessitam de uma série contínua de ciclos repetitivos, ou então um período mínimo de tempo de operação sem nenhum tipo de ajuste ou de perturbação, depois que qualquer ajuste interno ou externo tenha sido incorporado ao sistema. Por outro lado, qualquer ajuste em algum ponto do sistema irá sem dúvida afetar todas as correntes do sistema sem exceção, porém em diferentes intervalos de tempo.
Em sistemas tão complexos é geralmente possível observar os efeitos diretos de algum ajuste no processo, mas é muito mais difícil observar os efeitos indiretos de tal ajuste. Tal constatação é decorrente do fato de que tais sistemas raramente atingem um equilíbrio estável, pois continuamente ocorrem variações naturais ou induzidas no sistema. Por esta razão é indispensável compreender a importância de certos parâmetros operacionais controláveis e procurar gerenciar tais parâmetros com o objetivo de obter máxima capacidade de produção de açúcar com máxima recuperação da sacarose a um mínimo custo.
No caso da usina em questão pudemos logo constatar que realmente faltava capacidade no sistema de cozimento. Porém, a estação de cozimento e de centrifugação da massa B, até por ser mais antiga, estava em condições operacionais muito piores do que a correspondente estação da massa C. Os tachos de massa B tinham geometria mais inadequada do que os tachos de massa C e as centrífugas de massa C estavam padronizadas e operando bem, ao contrário das máquinas de massa B. O sistema de evaporação e sangrias também estava inadequado, produzindo xarope com um brix muito baixo para alimentar os tachos da massa A.
Para avaliarmos e controlarmos a recuperação da sacarose o parâmetro mais importante é a matéria seca contida na massa cozida no final de cada ciclo. A matéria seca no final de cada cozimento geralmente define o percentual de cristais que foram produzidos naquele ciclo e massas cozidas com brix final mais alto tem significativa influencia na diminuição de recirculação de materiais nos sistemas de cozimento. Já massas cozidas com baixo brix aumentam muito a recirculação de materiais reduzindo a capacidade dos equipamentos e também a recuperação da sacarose.
Embora relevante, o percentual de cristais na massa cozida não é o único parâmetro a ser observado. A dimensão dos cristais e a sua distribuição (CV) são muito importantes para um bom trabalho nas centrífugas. Cristais muito pequenos ou com alto CV provavelmente vão exigir mais lavagem nas telas e em consequência podem aumentar as perdas no mel e reduzir a recuperação. E certamente vão produzir mais recirculação de materiais.
Voltando à usina em questão, a nossa recomendação foi adiar a instalação do tacho contínuo de massa C para antes colocar ordem nos cozimentos de massa A e de massa B. Seria impossível corrigir no cozimento de massa C toda a recirculação de materiais que estava ocorrendo nas massas A e B com perda de capacidade e de recuperação.
A nossa recomendação foi antes investir na evaporação para garantir um xarope com brix adequado e desta maneira buscar uma alta recuperação já na massa A, dentro do princípio de evitar ao máximo a recirculação de materiais. E de forma simultânea obter capacidade de sangria de vapor vegetal V2 e V3 que será usado nos cozimentos contínuos de massa B e de massa A.
A segunda etapa foi investir em um tacho contínuo de massa B, aumentando a capacidade da instalação e adequando os tachos em bateladas de B para serem utilizados na massa A. Tudo sempre seguindo o princípio de arrumar o processo na sequencia natural do mesmo. Nesta mesma etapa seriam padronizadas as centrífugas de massa B de maneira a não estragar um bom trabalho de recuperação da sacarose que deveria ser obtido com o novo tacho contínuo.
Na terceira etapa, aí sim, instalar o tacho contínuo de massa C, com aumento de capacidade de produção e com toda a casa arrumada nas etapas anteriores do processo e disponibilizando mais tachos em bateladas para a massa A e/ou refinaria. Chegamos assim à etapa desejada com o mínimo indispensável de recirculação de materiais no processo.
A última etapa, opcional do ponto de vista econômico, seria a eventual instalação de cristalizadores verticais visando baixar a pureza do mel final entre 3 a 4 pontos. A questão é econômica porque o investimento é alto e há sempre a alternativa de continuar produzindo um pouco a mais de etanol. Depende do preço do açúcar, que não anda lá grande coisa nos últimos tempos em relação aos preços de etanol.
Este exemplo prático serve para demonstrar que não conseguimos obter uma boa recuperação apenas instalando o cozimento de massa C. Assim como uma boa extração na moenda começa com o primeiro terno operando bem, no setor de cozimento uma boa recuperação começa no cozimento de massa A.
Embora no Brasil a produção de açúcar seja geralmente feita com duas massas, todos os princípios fundamentais também se aplicam da mesma maneira.