Olhando para Frente
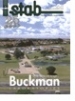
A nossa Revista STAB está de parabéns pelos 25 anos de circulação ininterrupta. É realmente um marco, e estamos orgulhosos de poder colaborar com uma pequenina parte deste grande esforço.
O pessoal da STAB nos pediu um relato dos avanços e transformações que a nosso ver ocorreram nestes últimos anos no Brasil. São sem dúvida notáveis.
Eu particularmente saí do Brasil para visitar outro país açucareiro de tradição pela primeira vez em 1977. O país em questão era a África do Sul. Comparando o que vimos com a realidade do Brasil daquela época, o nosso atraso tecnológico era gritante.
Tenho retornado à África do Sul em anos recentes, e a situação se inverteu completamente. Embora o Brasil seja um país muito grande e cujas usinas apresentam os mais variados níveis de avanço tecnológico, as nossas indústrias mais modernas e bem administradas não ficam devendo nada quando comparadas com as boas empresas dos países canavieiros mais avançados. O Brasil é hoje um exemplo no mundo para quem busca desenvolver uma agroindústria canavieira eficaz.
Tudo isto foi fruto de muito trabalho dos técnicos brasileiros. Mas este trabalho não pode parar. Assim, talvez melhor do que escrever sobre o passado, seria procurar empolgar os nossos jovens técnicos brasileiros que estão entrando neste setor para vencer os desafios que temos pela frente.
Quando comecei a trabalhar em uma usina em 1973, a razão social da empresas do setor era tipicamente Usina Santa Fulana Açúcar e Álcool. Hoje em dia, as novas empresas que estamos projetando chamam-se via de regra Empresa Sicrana Açúcar, Álcool e Energia. Esta é a palavra chave daqui para frente: bioenergia. As usinas do futuro terão que ser desenhadas e operadas com a perspectiva de serem muito eficientes em termos de energia.
Quando focamos os outros dois produtos, açúcar e álcool verificamos, que o processo para a produção de açúcar já atingiu uma razoável eficiência do ponto de vista energético. Ou seja, no processo para produção de açúcar há relativamente pouca margem para ganhos em energia e os técnicos conhecem sobejamente os caminhos que devem tomar. É mais uma questão econômica do que técnica: quanto vale a pena investir para termos o retorno em energia excedente. Este estágio tecnológico é em grande parte devido aos países produtores de açúcar de beterraba. Como a indústria de beterraba necessita de combustível para a produção de açúcar, devemos sempre verificar o que este povo anda fazendo para procurar adaptar a tecnologia para as nossas condições econômicas específicas.
Já o processo para a produção de álcool que usamos no Brasil é extremamente perdulário em uso de energia. Há perspectivas enormes para obtermos economia de energia na produção de álcool carburante a partir da cana.
Basicamente temos três linhas de atuação. A primeira e que traz mais benefícios é sem dúvida procurar trabalhar com teor alcoólico mais alto no vinho que vamos destilar, pois o consumo de vapor depende de quanta água enviamos para o aparelho. Menor consumo de vapor significa menor consumo de água e por conseqüência menor consumo de energia elétrica.
Para trabalharmos com altos teores de álcool no vinho, na faixa de 13-15% em volume e acima, é imprescindível poder controlar a temperatura da fermentação. Para controlar a temperatura da fermentação temos que produzir água gelada por meio de chillers. Os chillers por compressão não são adequados, pois vão usar grandes quantidades de energia elétrica excedente que queremos justamente exportar. A melhor escolha é o uso dos chillers por absorção (similares à geladeira a gás). Os chillers por absorção produzem água gelada a partir de alguma fonte de calor, que inclusive pode ser pobre, com temperatura na faixa de 85 ºC a 95 ºC. E as usinas de cana são uma fonte inesgotável de fontes pobres de calor não aproveitado: condensados contaminados, vinhaça, flash de vapores diversos, água dos lavadores de gases, vapor V3, etc.
Os chillers por absorção de grande capacidade são equipamentos ainda importados, mas isto não é problema porque praticamente não tem peças móveis, apenas uma pequena bomba para extração do ar do sistema na partida. Apresentam um baixo custo de operação, porque vão usar energia atualmente desperdiçada na maior parte dos casos.
Com fontes pobres de calor na faixa de 90-95 C podemos produzir água gelada na faixa de 22-23 ºC e assim garantir temperaturas na fermentação abaixo de 30 ºC. Com estas temperaturas é possível trabalhar com 15% GL sem perdas de eficiência. Vinhos com 15% de álcool em volume produzem muito menos vinhaça, e o retorno do investimento deve levar em conta também a economia nos custos de distribuição de vinhaça na lavoura, os quais podem ser significativos.
Uma vez obtidos vinhos com alto teor alcoólico, a segunda linha de atuação é procurar trabalhar com aparelhos de destilação mais econômicos em vapor. Isto é possível adotando-se aparelhos que trabalham em duplo efeito (destilação sob vácuo), ou seja, os vapores alcoólicos de uma coluna são usados para aquecer outra coluna operando com pressão mais baixa (vácuo). Embora sejam equipamentos de custo mais elevado, já são utilizados em países que necessitam economizar energia, sendo portanto uma tecnologia consolidada. Novamente é mais uma questão econômica do que técnica: em quanto tempo o investimento deve retornar. O consumo típico de vapor para produzir álcool hidratado em um aparelho convencional com vinho de 9% GL, de 2,2 a 2,4 t/m3, passa para 1,2 a 1,4 t/m3 em um aparelho em duplo efeito. Uma economia significativa.
A terceira linha de atuação visa economizar energia na desidratação. É onde o ganho relativo será menor, pois apenas uma parcela da produção de álcool será desidratada. O uso do MEG como agente desidratante e o uso de peneiras moleculares (zeólitos) já são uma realidade no Brasil, embora a grande maioria do álcool anidro aqui produzido ainda seja por meio de ciclo hexano, com maior consumo de vapor. Por outro lado, temos que estar atentos à nova tecnologia de membranas poliméricas especiais que trabalham com misturas hidroalcoólicas na fase vapor, podendo produzir álcool anidro a partir de flegmas com grande economia de vapor. As possibilidades são inúmeras. Há muita pesquisa em andamento.
Resta lembrar que esta enorme economia potencial de energia na produção de álcool não visa tão somente vender mais energia elétrica excedente para a rede. O mundo inteiro, inclusive o Brasil, pesquisa processos adequados para a produção de etanol a partir de materiais celulósicos, sendo o bagaço uma das possíveis matérias primas. Como o bagaço é a nossa fonte primária de energia na indústria, urge adotar processos que usem cada vez menos bagaço para passar a produzir etanol do mesmo quando houver processos econômicos para esta finalidade.
Para completar, embota tenhamos focado a economia de energia na produção do álcool, é importante mencionar outros aspectos importantes visando eficiência energética, que naturalmente valem tanto para açúcar como para álcool.
A eletrificação das usinas será também uma realidade incontestável para que maiores contingentes de energia elétrica sejam exportados. Caldeiras mais eficientes e com pressões e temperaturas mais elevadas serão a regra daqui para frente.
Já foram comercializadas no Brasil as primeiras moendas que operam sem bagaceira e sem rolo de saída, sendo que o projetista sugere economia de cerca de 20% no consumo de energia. Se estes equipamentos na prática apresentarem eficiência de extração similar às moendas convencionais, será uma nova revolução em matéria de economia de energia.
Escrevemos este texto pensando em motivar os novos técnicos que começam a trabalhar em nosso setor. Há muito o que fazer para melhorar. Embora o Brasil seja hoje uma referência mundial em termos de produção de bioenergia, não podemos em hipótese nenhuma ficar sentados em cima da nossa fama. Certamente foi muito mais fácil chegar até aqui do que será manter a nossa posição de destaque, pois agora o mundo está de olho em nós.
Portanto, mãos à obra. Esperamos ter muito o que conversar nos 50 anos da STAB.