Instalação de Turbinas a Vapor de Grande Porte
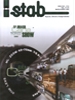
Turbo geradores de até 60 MW já fazem parte de vários projetos de cogeração no setor canavieiro. A instalação destas máquinas traz muitas vezes desafios específicos, cujas soluções podem variar dependendo de cada fabricante e de cada arranjo físico em particular. Nossa idéia hoje é discutir alguns casos peculiares que temos vivenciado recentemente.
Podemos começar discutindo a respeito da necessidade de válvula de retenção na tubulação de vapor de escape em máquinas de contrapressão. Dependendo do fabricante, recebemos fluxogramas recomendando a instalação, na tubulação de escape, de válvulas de bloqueio e de retenção.
Temos questionado sistematicamente a exigência desta válvula de retenção, pois via de regra estamos falando de tubulações com diâmetro acima de 750 mm. Trata-se de um acessório pesado, que deve ser instalado em trechos horizontais da linha, encarecendo os suportes de mola e que necessita de acessos especiais para fins de manutenção. A questão é: necessitamos desta válvula?
A função de uma válvula de retenção é garantir o fluxo do fluido em um sentido único da tubulação. Quando há turbinas operando em paralelo, se uma delas parar abruptamente, pode ocorrer entrada de vapor de escape na turbina que foi desarmada pelo fechamento da sua válvula de fecho rápido. Imaginando a carcaça da turbina como uma parte da tubulação, fica evidente que não pode haver fluxo de vapor de escape em sentido contrário se a válvula de fecho rápido está bloqueada. Mesmo numa situação hipotética de partida simultânea de várias turbinas, que estejam com suas válvula de fecho rápido abertas, não haveria fluxo de vapor em sentido contrário porque a pressão do vapor vivo é sempre mais alta.
Concluímos assim que esta válvula de retenção na tubulação de escape é desnecessária, e temos recomendado aos clientes não instalar. Caso seja uma turbina de emergência, que deve estar sempre aquecida e pronta para uma partida rápida, basta garantir um sistema adequado para a drenagem de condensado formado por resfriamento. É bom lembrar que a válvula de retenção não evitaria a formação deste condensado, porque tais válvulas não são 100% estanques e sempre haveria pequeno vazamento de vapor.
Já a válvula de retenção na linha de saída da extração controlada da turbina, esta sim, ao contrário, é indispensável.
O caso típico são turbinas de alta pressão com extração controlada a 22 bar, por exemplo para atender aos coletores de vapor vivo das turbinas de moendas. Neste caso, se a turbina é desarmada pelo bloqueio da válvula de fecho rápido e se não houver bloqueio adequado na linha de extração controlada, vapor de 22 bar vai entrar na carcaça da turbina. Novamente, imaginando a carcaça da turbina como uma parte da tubulação, temos vapor a 22 bar na entrada e vapor a 2,5 bar na saída, ocorrendo um fluxo intenso de vapor. Se o gerador tiver sido desarmado também, será um acidente grave na certa, pois a turbina vai disparar, já que está sem carga no seu eixo e sem controle de vapor na entrada. Neste caso, toda redundância para evitar uma situação destas será bem vinda.
Portanto, nas tomadas de extração das turbinas, evitar o fluxo de vapor em sentido contrário é indispensável. Temos recomendado a instalação de válvulas de retenção nestas linhas, mas os resultados não têm sido muito animadores. Como a vazão de vapor pode variar, dependendo das condições do processo, estas válvulas operam de forma intermitente a apresentam cedo problemas mecânicos.
Decidimos recentemente preconizar, como solução para este problema, a utilização de válvulas específicas para esta finalidade. São válvulas especiais (“Extraction Check Valve”), desenhadas especificamente para a aplicação em tomadas de extração de turbinas. Estas válvulas têm por finalidade impedir o fluxo reverso de vapor na linha de extração, e podem ter atuadores que operam com ar comprimido ou com óleo, e ter também sistemas de contrapeso para fechamento rápido pela ação da gravidade em caso de falhas. Devem ter como características vedação positiva (aumentada pela pressão do vapor), fechamento rápido e perda de carga muito baixa.
É importante lembrar que nem todas as tomadas de turbinas exigem este tipo de acessório. Quando são tomadas sem extração controlada, por exemplo para aquecimento de condensado (ciclo regenerativo), cujo vapor extraído vai ser usado em trocadores de calor, e desde que não existam linhas de vapor de pressão mais elevada ligadas nestes coletores, não há possibilidade de geração de fluxos invertidos de vapor, e assim sendo tais acessórios não serão necessários.
Outro aspecto importante na instalação destas grandes turbinas é garantir facilidades para as operações de sopragem das linhas de vapor. Como estes equipamentos podem ficar parados na entressafra de quatro a cinco meses todos os anos, as operações de sopragem são muito mais freqüentes do que em centrais termoelétricas que operam de forma contínua.
Para facilitar estas operações, passamos a recomendar a inclusão no escopo de fornecimento das turbinas a vapor, de dispositivos de sopragem que permitem esta operação sem a remoção da tubulação de vapor vivo.
São dispositivos similares aos que já existem para a sopragem de linhas que atendem às válvulas condicionadoras de vapor, os quais permitem a retirada do corpo da válvula de fecho rápido, possibilitando assim a sopragem da linha sem nenhuma intervenção na mesma.
Com as sobras de bagaço e o advento do uso da palha, existe a tendência de aumentar o número de instalações de turbinas de condensação. Surge então a questão de como instalar o condensador que está sob alto vácuo.
O arranjo tradicional é o condensador montado sob a turbina, já que desta maneira a tubulação de vapor da turbina até o condensador fica reta e curta, bastando uma junta flexível entre os equipamentos.
Com este arranjo, para que não existam equipamentos abaixo do nível zero, a turbina deve ser montada com cerca de 9.000 mm de altura, encarecendo a base e o respectivo prédio. O custo adicional do prédio pode ser compensado se conseguirmos usar todos os espaços disponíveis de uma maneira racional, instalando equipamentos elétricos diversos tais como transformadores, cubículos de alimentação, gerador diesel, compressores, etc.
Se o equipamento for montado com 5.000 mm de altura, dimensão típica para turbinas de contrapressão, então será necessário construir um fosso para a instalação do sistema de remoção do condensado sob vácuo da turbina de condensação. Esta solução pode ser adequada se o solo em questão não apresentar dificuldades na escavação (rochas, por exemplo) e se o lençol freático for baixo, não criando assim grandes problemas de impermeabilização do fosso. Ter equipamentos abaixo do nível zero, neste caso específico, não é um grande problema, porque se trata de um ambiente limpo, geralmente pressurizado, e uma simples bomba tipo sapo para drenar eventuais vazamentos resolve a questão.
Portanto, tanto a solução com 5 m ou com 9 m de altura da base pode ser adequada, depende de estudarmos os prós e contras caso a caso.
Entretanto, para instalarmos turbinas de condensação em espaços apertados de instalações já existentes, é importante lembrar que o condensador também pode ser montado ao lado da turbina. Neste caso, a saída de vapor é por cima da máquina, e a tubulação de vapor terá um comprimento maior. Esta solução permite certa flexibilidade de alternativas de montagem, porém a tubulação sobre a turbina sempre vai dificultar as operações de manutenção com a ponte rolante.
Uma outra alternativa são as turbinas de condensação com condensadores “axiais”, ou seja, o vapor sob vácuo deixa a turbina na direção do eixo da turbina e entra no condensador que está alinhado com a mesma.
Todas estas possibilidades de montagem ganham ainda mais possíveis variações se decidirmos instalar os turbo geradores ao tempo. E por que não? As turbinas de grande capacidade já possuem uma carenagem para reduzir ruído e para evitar perda de calor, e tais carenagens podem ser projetadas para trabalhar ao tempo. O mesmo vale para o gerador. O redutor de velocidade não é diferente daqueles que operam ao tempo no sistema de preparação de cana, por exemplo. Nesta situação, a manutenção pode ser feita por guindastes que teriam acesso fácil aos equipamentos, e os prédios seriam bem mais leves apenas para conter os equipamentos elétricos e eletrônicos.
Esta solução já existe no exterior. Quem será o primeiro a adotá-la nas usinas do Brasil?