Exportação de energia elétrica X Consumo de energia térmica
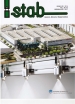
A discussão a respeito de aumentarmos a exportação de energia elétrica, através da redução do consumo de vapor no processo, vez por outra volta à mesa, como ocorreu por exemplo em um estudo conceitual que estava em andamento e que acabou definindo o tema deste texto.
Quando tomamos a decisão de investir para baixar o consumo de vapor no processo, podemos aumentar a exportação específica de energia em kWh/tc, mas ao fazermos isso, paradoxalmente, estamos utilizando menos bagaço em um ciclo termodinâmico mais eficiente (cogeração) e mais bagaço em um ciclo termodinâmico menos eficiente (geração pura). A usina torna-se mais eficiente na exportação de energia elétrica, um produto que corresponde geralmente de 10% a 15% do seu faturamento bruto. Mas terá sido um bom investimento, ou haveria outras alternativas mais eficazes do ponto de vista econômico-financeiro?
Os produtos principais, açúcar e etanol, tem seus preços bem correlacionados em função do preço do ATR e das condições do mercado. Já a formação de preço da energia elétrica, a qual cada vez mais tenderá a ser negociada no mercado livre, é dependente de inúmeros outros fatores e deve ser levada em conta na tomada de decisão do investimento. A respeito de buscarmos eficiência e/ou eficácia, discorremos no texto da Revista STAB da edição julho/agosto de 2017 (Redução de Custos, Eficiência, Eficácia, Excelência).
Com certa frequência ouvimos o argumento de que na usina de cana a energia elétrica exportada tem custo desprezível e, portanto, preços baixos de energia não seriam um problema. Não concordamos, mas também sabemos que é extremamente difícil reunir critérios definitivos para arbitrar os custos de produção de energia elétrica e de energia térmica em uma central de cogeração. A esse respeito, já discorremos no texto da Revista STAB da edição maio/junho de 2019 (Custo da Energia Elétrica x Custo Líquido do ATR).
A matéria prima cana de açúcar tem suas desvantagens, como por exemplo conter 70% de água e assim ser muito perecível, não podendo ser armazenada. Porém, do ponto de vista da energia necessária para a sua produção e o seu processamento, a cana é muito superavitária em energia.
Nas operações de CTT (Colheita, Transbordo e Transporte) o consumo de energia mecânica pode ser estimado em função do consumo médio de óleo diesel, o qual varia entre 3,0 e 4,0 litros por tonelada de cana (l/tc), sendo as faixas típicas de consumo 0,8 a 1,5 l/tc na Colheita, 0,7 a 0,9 l/tc no Transbordo e 1,4 a 2,0 l/tc no Transporte.
Convertendo, de forma aproximada, estas quantidades de óleo diesel em kWh consumido em função da potência média dos motores, chegamos em uma demanda típica de energia mecânica entre 30 a 40 kWh/tc.
Não temos informações específicas sobre plantio e tratos culturais, mas a agregação destas operações provavelmente não deve elevar este parâmetro acima de 45 kWh/tc, um valor que usinas modernas atendem sem dificuldades, para a hipótese de um dia todos estes veículos serem acionados por motores elétricos. Caso no futuro os motores adotados não sejam elétricos, o potencial de produção de biogás das usinas também permitiria substituir toda a energia correspondente ao óleo diesel usado no CTT.
Embora sistemas de irrigação da cana não sejam muito utilizados no Brasil, na nossa experiência profissional o maior parâmetro de energia requisitado para irrigação no Brasil esteve na faixa de 20 kWh/tc, valor que também cabe dentro do potencial energético da cana.
Nas operações industriais, em função da grande quantidade de água contida na cana e notadamente nas operações de evaporação e de destilação, a demanda de energia térmica para o seu processamento (85% a 90% do total) é muito maior do que a demanda de energia mecânica (10% a 15% do total). A energia mecânica para processar a cana na indústria varia entre 25 kWh/tc e 35 kWh/tc, por coincidência valores próximos àqueles das operações de CTT. A energia térmica para processar a cana, com consumo de vapor de processo típico de 41% (410 kg/tc), na mesma unidade corresponde aproximadamente a 250 kWh/tc, ou seja, 89,3% do total na média.
A energia térmica total fornecida pela queima do bagaço de cana com fibra entre 12% e 14%, sem trazer nenhuma palha adicional, varia na faixa entre 540 e 620 kWh/tc. Valor acima, portanto, das necessidades energéticas para a produção e o processamento da cana. Já a energia térmica fornecida pela produção de biogás, dependendo do mix de produção açúcar/etanol e da utilização de torta de filtro, pode variar entre 35 e 75 kWh/tc.
Há mais ou menos 20 anos era ainda possível encontrarmos usinas consumindo 50% (500 kg/tc) de vapor no processo, principalmente aquelas que não exportavam energia elétrica ou que não tinham um mercado para a venda de bagaço excedente. Com o início da exportação de energia elétrica o consumo de vapor no processo foi sendo gradualmente reduzido até chegar hoje em dia no valor médio na faixa entre 38% e 42%.
O tema deste texto nos remete assim à seguinte questão:
“Seria eficaz procurar baixar o consumo de vapor de processo para a faixa entre 36% e 30%?”.
A resposta a esta questão seria buscar um eventual ponto de equilíbrio técnico/econômico na combinação de um Ciclo Rankine de Cogeração, com eficiência global na faixa entre 65% e 70%, no máximo, com um Ciclo Rankine de Geração Pura, com eficiência global na faixa entre 25% e 30%, no máximo. A respeito da eficiência de ciclos termodinâmicos, também discorremos no texto da Revista STAB da edição novembro/dezembro de 2008 (Ciclos de Cogeração).
Vamos simular algumas hipóteses considerando uma cana com 12,5% de fibra média, sem palha, gerando vapor motriz com 68 bar(a) e 525 oC em caldeiras tradicionais com grelha e com uma GEV média estimada em 2,10 kg vapor/kg bagaço. Para estimar o tempo médio da safrinha (geração de energia elétrica durante o período da safra quando há falta de cana ou manutenção), consideramos as mesmas premissas adotadas no estudo relatado no texto da Revista STAB da edição abril/junho de 2020 (Vinhaça: Biodigestão x Incineração), as quais consideram também que todo o bagaço disponível seria queimado na safra e na safrinha.
No caso extremo máximo de 50% de consumo de vapor de processo, quase toda a energia térmica (91,7%) disponível no bagaço é utilizada apenas em um ciclo de cogeração, com pouca energia parasita necessária nas torres de resfriamento para garantir a condensação de vapor sob vácuo, e com o menor investimento em equipamentos, seja na UTE, seja no processo.
No caso extremo mínimo de 30% de consumo de vapor no processo, 59,5% da energia térmica disponível no bagaço é utilizada no ciclo de cogeração e 40,5% da mesma é utilizada em um ciclo de geração pura, e com muito maior necessidade de investimento em equipamentos.
Nas situações mais encontradas nas usinas, de consumo de vapor no processo na faixa de 40%, cerca de 75,6% da energia térmica disponível no bagaço é utilizada no ciclo de cogeração e 24,4% da mesma é utilizada em um ciclo de geração pura.
A tabela indicada na Figura 1 mostra o acréscimo percentual da exportação anual de energia elétrica em relação ao caso base, destacado em negrito, quando vamos de um ciclo com 91,7% de cogeração para um ciclo com 59,5% de cogeração, tendo como referência a energia térmica contida no bagaço correspondente a uma cana com 12,5% de fibra. É possível verificar que, para uma significativa redução de 40% no consumo de vapor de processo, de 500 kg/tc para 300 kg/tc, há um acréscimo de 18.5% na exportação de energia elétrica.
Figura 1 - Variação percentual dos parâmetros
O diagrama indicado na Figura 2 traz uma representação gráfica dos valores da tabela acima, sendo interessante verificar que até a faixa de 400 kg/tc de consumo de vapor de processo, há uma ligeira redução percentual da energia elétrica consumida, fruto principalmente da adoção típica de maior sangria de vapor vegetal V1, V2 e V3, pois quanto maior o nível de sangria, menor é a condensação de vapor no último efeito da evaporação e, portanto, menor consumo de energia nas torres de resfriamento. Para reduzir ainda mais o consumo de vapor de processo é necessário, na sequência, adotar sistemas de regeneração de calor, o que aumenta o consumo percentual de energia elétrica em função da necessidade de bombeamentos com maior perda de carga e de equipamentos adicionais no processo.
É também possível verificar que para consumos de vapor de processo entre 500 e 400 kg/tc há um certo descolamento vantajoso entre a energia gerada e a energia exportada, mas entre 400 e 300 kg/tc já não existe mais um ganho tão representativo.
Figura 2 - Acréscimo de exportação de Energia Elétrica
Os números aqui apresentados de certa maneira demonstram o consenso natural do mercado no sentido de adotar o consumo de vapor de processo na faixa de 40% como sendo o mais eficaz do ponto de vista econômico e financeiro. Mas quais poderiam ser as alternativas de investimento possíveis?
A tabela da Figura 1 mostra que, para as premissas adotadas, vamos exportar cerca de 6.000 MWh a mais se houver investimentos para passar o consumo de vapor de processo de 400 para 350 kg/tc.
Mas note-se que este valor adicional de exportação corresponde a cerca de 7% do consumo de energia na indústria. É possível imaginar, apenas como exemplo, que um plano bem conduzido para redução de consumo de energia elétrica, com a adoção por exemplo de motores de alta eficiência, de inversores de frequência e de boas práticas operacionais, consiga uma redução de consumo de energia na faixa de 10%. Este investimento seria provavelmente mais eficaz, garantindo os mesmos 6.000 MWh por safra de exportação adicional, sem complicações no processo e sem investimentos na UTE.
Por outro lado, é importante ter sempre em mente que o ciclo de condensação com geração pura de energia significa um grande desperdício de energia térmica, e assim é indispensável verificar se não existe alguma maneira de transformar esta energia térmica perdida em receitas para a empresa. Uma alternativa clássica é produzir etanol de milho junto com o processamento da cana, mas qualquer outro processo que utilize energia térmica poderia eventualmente ser interessante.
Concluindo, insistimos que os estudos aqui simulados valem apenas para as premissas correspondentes adotadas. Eventual instalação, por exemplo, de condensador evaporativo no turbo gerador de condensação vai reduzir o consumo de energia parasita no ciclo de geração pura.
Desta maneira, o caso específico de cada usina deve ser estudado detalhadamente, para termos a certeza de que não existem alternativas melhores do que baixar o consumo de vapor de processo apenas com o objetivo de aumentar a exportação de energia elétrica.