Custo da energia elétrica X Custo líquido do ATR
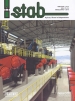
Recentemente durante um Seminário da STAB em Piracicaba o engenheiro Zarpelon nos fez uma daquelas típicas perguntas que valem um milhão de dólares e para as quais ainda não encontramos uma resposta definitiva e convincente: “Quanto custa produzir um kWh na usina?”
Pretendemos assim discorrer sobre as especificidades e as dificuldades em determinar este custo e sobre procedimentos alternativos que são usados em outros setores da agroindústria.
As unidades agroindustriais produtoras de açúcar utilizam ciclos termodinâmicos de cogeração, ou seja, a partir de um mesmo combustível produzem energia térmica e energia mecânica, esta última podendo ser fornecida por motores elétricos ou por turbinas a vapor.
Uma agroindústria processando beterraba na Europa com combustível fóssil utiliza um ciclo de cogeração tanto quanto uma agroindústria processando cana no Brasil que exporta energia elétrica excedente, com a diferença de que lá o preço do combustível não justifica do ponto de vista econômico a exportação de energia.
Como o ciclo de cogeração pressupõe o uso de um único combustível para produzir os dois tipos de energia, na prática é difícil alocar custos para a produção de vapor (energia térmica) e de energia elétrica (mecânica), já que além do combustível em comum existem também os equipamentos em comum (caldeiras, turbo geradores e sistemas auxiliares).
Como arbitrar os custos do pessoal de operação e de manutenção das caldeiras e dos turbo geradores? Como separar os custos do tratamento de água das caldeiras? Como dividir os custos para manuseio e armazenamento do bagaço excedente? São perguntas que na prática não tem respostas convincentes.
No caso da cana de açúcar pode haver uma estimativa real do custo do kWh quando existem turbo geradores de condensação ou quando a usina pratica de forma intensiva a condensação caipira (atmosférica), já que nos ciclos de condensação sem extração não há uso de energia térmica no processo sendo, portanto, ciclos termodinâmicos para geração exclusiva de energia elétrica.
Admitindo que necessitamos de aproximadamente 760 horas (um mês) para a inspeção anual das caldeiras, temos no máximo 8000 horas de operação da UTE da usina. Destas 4800 a 5000 h são o período efetivo da safra (moagem regular), 800 a 1000 h são o período da “safrinha” (período com moagem interrompida e produção de energia elétrica a partir de bagaço excedente, durante e após a liquidação do processo) e aproximadamente 2000 h são o período de entressafra (produção exclusiva de energia elétrica a partir de bagaço excedente).
Desta maneira poderia haver geração exclusiva de eletricidade no máximo durante um terço do período anual de operação da UTE. Apenas neste período seria possível determinar com precisão o custo do kWh, mas de novo surgem questões difíceis de serem respondidas.
Os sistemas e equipamentos estariam operando na safrinha e entressafra com sua máxima eficiência, de maneira a buscar o mínimo custo do kWh? Caldeiras operando com baixa capacidade terão energia parasita mais alta e geralmente entregam vapor motriz com temperatura mais baixa. Turbo geradores operando com baixa capacidade geralmente tem eficiência mais baixa. Estes aspectos tem a tendência de prejudicar o custo do kWh produzido nos ciclos de condensação, seja a vácuo, seja caipira.
Qual o custo do bagaço excedente usado como combustível? Palha adicional foi trazida durante a safra?
O bagaço pode ser considerado como um resíduo, ou seja, quando se processa cana o bagaço será necessariamente produzido. Mas trazer palha adicional pode ter um custo representativo no preço final da cana.
O custo do bagaço pode ser estimado pelo seu preço de oportunidade para venda a eventuais terceiros. Este preço geralmente é definido pelo mercado em função do seu poder calorífico para a produção de vapor (energia térmica) e em função do preço de outros combustíveis eventualmente disponíveis. Entretanto, há compradores usuais de bagaço que o utilizam em ciclos de cogeração, tornando-o mais competitivo em comparação com o seu uso para um ciclo de geração pura na entressafra.
Verificamos que o período de tempo relativo, no qual teoricamente seria possível estimar com mais precisão o custo do kWh, corresponde a no máximo um terço da operação total da UTE, com possibilidade de operação com baixa eficiência. Já nos dois terços restantes as estimativas tornam-se muito mais complexas.
Uma primeira questão relevante é definir o nível de exportação de energia elétrica da UTE, já que uma mesma quantidade de cana pode exportar mais ou menos kWh/tc, alterando drasticamente a economicidade da operação. As questões técnicas referentes a este aspecto foram comentadas há dois anos no texto da Revista STAB de Maio/Junho de 2017.
Estivemos desenvolvendo recentemente uma avaliação técnica comparativa entre diversas usinas e para fins de classificação definimos um critério qualitativo para definir nível baixo / médio / alto de exportação de energia elétrica, considerando que não havia queima de palha adicional.
Consideramos nível baixo de exportação até 30 kWh/tc. São tipicamente usinas usando vapor motriz com temperatura na faixa de 350-400 oC e sem turbo gerador de condensação.
Consideramos nível médio de exportação entre 30 e 55 kWh/tc. São tipicamente usinas já usando vapor motriz na faixa de 480-525 oC, porém que ainda possuem caldeiras antigas em operação e sem turbo gerador de condensação.
Consideramos nível alto de exportação acima 55 kWh/tc, podendo chegar até 70 kWh/tc ou mais. São usinas usando todo o vapor motriz em alta temperatura e com turbo gerador de condensação.
O nível de exportação de energia elétrica é importante nesta análise porque máxima produção de açúcar e/ou etanol e máxima exportação de energia elétrica numa mesma usina são parâmetros conflitantes. A máxima exportação de energia elétrica pressupõe reduzir ao mínimo o consumo de vapor no processo, para aumentar a geração no ciclo de condensação. O mínimo consumo de vapor no processo pressupõe muita sangria de vapor vegetal V1 e V2, resultando em sistemas de evaporação onde a degradação da sacarose aumenta em função do maior tempo de residência do caldo submetido a altas temperaturas.
A perda de sacarose no processo quando buscamos maximizar a produção de energia elétrica é outro fator que causa incertezas na avaliação do custo da energia, pois há na prática uma troca parcial das receitas dos produtos finais da usina. Sem deixar de mencionar que uma usina que esteja com caldeiras com capacidade limitada, mesmo não exportando energia, pode eventualmente sofrer do mesmo mal.
Outro aspecto de conflito bem conhecido é o nível de embebição no processo de extração do caldo. Devemos aumentar a embebição para ter melhor extração (maior produção de açúcar) ou devemos reduzir a embebição para aumentar o poder calorífico do bagaço (maior exportação de energia)?
Os custos operacionais diretos fixos mais relevantes na indústria, sem levar em contar administração geral, amortização de capital e depreciação, são em ordem decrescente o pessoal, a manutenção e a energia elétrica da concessionária inclusive na entressafra. A venda de energia não implica em maior necessidade de pessoal na indústria. A manutenção industrial aumenta apenas nas áreas de caldeiras e de turbo geradores. A conta da concessionária diminui quando há maior período de cogeração, compensando pelo menos em parte o sobre custo da manutenção e desde que seja uma usina moderna de projeto recente.
Os custos operacionais variáveis para a movimentação do bagaço excedente para uso na safrinha e na entressafra não devem variar muito se o bagaço for carregado em caminhões para venda a terceiros ou se for carregado na esteira dosadora para exportação de energia adicional.
Colocadas todas as premissas a respeito do tema podemos voltar agora à questão original de como calcular o custo do kWh. Como o bagaço é um resíduo e o seu custo só pode ser estimado pelo preço de oportunidade da sua eventual venda a terceiros, a nossa sugestão é usar para efeitos comparativos um sistema similar ao que é usado em outros setores agroindustriais que também produzem diversos subprodutos, como é o caso da energia elétrica em relação à cana de açúcar.
O caso, por exemplo, de plantas que processam milho visando a produção de amido. Estas plantas produzem, além do amido que é o produto mais valioso e que define a rentabilidade da indústria, inúmeros outros subprodutos tais como óleo vegetal, farelo, etc. Neste caso é usado o conceito assim denominado “Preço Líquido do Milho”, já que o milho é uma commodity. Em vez de produzir intermináveis discussões para determinar o custo de produção de cada subproduto que geralmente não vão produzir nenhum consenso, eles descontam do preço da matéria prima o valor da venda líquida de cada subproduto. Exemplificando, se uma tonelada de milho após processamento produzir 30% de farelo que é vendido com preço equivalente a 50% do preço do milho, então o preço líquido do milho naquela planta específica é reduzido em 15%. Quanto menor é o preço líquido da matéria prima mais rentável é a planta, já que no caso de commodities quem define os preços de venda é o mercado, não o vendedor colocando uma margem sobre o seu custo.
No caso das usinas o preço da cana corresponde aproximadamente a 70% do custo de produção de açúcar e/ou etanol que tem valores de mercado mais ou menos atrelados. Na prática, 70% do custo destes produtos corresponde ao preço do ATR necessário para se produzir uma tonelada de açúcar ou um metro cúbico de etanol.
Do ponto de vista prático é necessário estimar para cada nível de exportação de energia elétrica qual seria a redução do preço líquido do ATR necessário para a produção de açúcar e/ou etanol, sem deixar de levar em conta a eventual perda ou degradação da sacarose no processo, que pode ser maior ou menor dependendo do nível de exportação de energia elétrica.
Da mesma maneira é necessário estimar qual seria a redução do preço líquido do ATR para uma eventual venda de bagaço excedente total ou parcial. Por exemplo, usar bagaço excedente na safrinha mas vender o bagaço excedente que seria usado na entressafra.
Seria assim possível elaborar tabelas indicando qual seria a redução esperada do custo do ATR para cada condição típica específica de geração de energia ou de venda de bagaço.
Como açúcar e etanol também são commodities, cujo preço de venda por definição é determinado pelo mercado e não pelo seus custos de produção, empresas com menor custo de ATR serão sempre as mais competitivas.