Cogeração de Energia Elétrica com Difusor
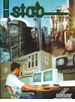
Estamos discutindo com um cliente, que pretende instalar uma nova linha para extração de caldo, se do ponto de vista da cogeração de energia elétrica, seria melhor instalar uma moenda ou um difusor.
Como uma instalação com difusor exige menor consumo de energia mecânica, à primeira vista a resposta imediata seria o difusor. Ocorre que, para se atingir as altas extrações obtidas com o difusor, necessitamos normalmente de maiores taxas de embebição, quando comparadas com as taxas usadas nas moendas. Portanto, uma análise mais detalhada de cada caso específico é indispensável.
Pelo menos em tese, tanto moenda como difusor exigem um sistema de preparo pesado (índice de preparo acima de 90%) para proporcionar um alto grau de extração. Entretanto, pelo menos no Brasil, a prática tem demonstrado que, para linhas de moenda com um mínimo de seis ternos, um sistema de preparo com desfibrador leve apresenta resultados satisfatórios. Em outras palavras, não encontramos na prática diferenças representativas de extração em moendas de seis ternos bem operadas quando são equipadas com desfibrador pesado ou com desfibrador leve.
Já para o difusor um preparo pesado é indispensável, o qual necessita de mais potência instalada.
Considerando uma linha nova processando 500 t/h de cana, teríamos tipicamente para a moenda um nivelador, um jogo de facas oscilantes e um desfibrador leve. Para o difusor teríamos um desfibrador pesado. Os consumos de potência no preparo da cana para a moenda e o difusor seriam de cerca de 2.600 kW e de 3.250 kW respectivamente. Estamos falando de potência média consumida, e não de potência instalada. Portanto por enquanto a vantagem seria da moenda, pelo menos para o caso específico da experiência brasileira.
Na linha de extração propriamente dita, temos que comparar inicialmente a potência de seis ternos contra a potência de um terno para secagem do bagaço. Temos ainda que lembrar que os primeiros ternos consomem mais potência do que os últimos, principalmente o primeiro em relação aos demais. Os consumos de potência para a moenda e difusor seriam de cerca de 4.600 kW e de 750 kW respectivamente. Aqui a vantagem é grande para o difusor.
Temos agora que comparar a potência consumida nos equipamentos auxiliares da moenda (quatro bombas de embebição, cinco esteiras intermediárias e peneiras rotativas) e do difusor (dezoito bombas de embebição, duas esteiras intermediárias, rolos pré desaguadores e acionamento principal). Estimamos que os consumos de potência para os equipamentos auxiliares da moenda e do difusor seriam de cerca de 200 kW e de 420 kW respectivamente.
Portanto o saldo positivo de potência exportável seria de aproximadamente 3.000 kW em favor do difusor ou, para uma safra com cerca de 4.000 h efetivas, uma venda anual adicional de cerca de 12.000 MW.h. Esta é uma comparação direta desfavorável para o difusor, já que na moenda normalmente usamos vapor a 20 ou eventualmente 40 bar, e o vapor motriz não usado no difusor poderia ser eventualmente gerado a pressão mais alta e passar por turbinas mais eficientes na casa de força, aumentando assim a diferença calculada.
A comparação acima diz respeito ao vapor motriz, mas agora é necessário discutir os aspectos referentes ao vapor de processo. Um dos argumentos em favor do uso do difusor é a sua maior extração, mas normalmente este maior nível de extração é obtido em parte devido ao maior nível de embebição. É mais fácil aplicar altas taxas de embebição em difusor do que em moenda, principalmente no Brasil, onde as taxas de moagem (fibra processada por volume de camisas, tf/h.m3) são muito elevadas.
Se considerarmos para o difusor uma taxa de embebição similar à da moenda, por exemplo 250% sobre fibra, as extrações serão mais ou menos equivalentes, e neste caso a nossa comparação se encerra por aqui. O difusor ganha.
Admitindo que se queira extrair mais com difusor pelo aumento da taxa de embebição, por exemplo passando para uma embebição de 300% sobre a fibra (valor usual em difusores no Brasil), vamos produzir mais caldo misto em relação à cana, passando de cerca de 105% para 112%. Isto significa enviar 35 t/h de água a mais para o processo, no caso da nossa moagem de 500 t/h.
Agora é preciso analisar o perfil da planta de cogeração prevista, para avaliar o eventual estrago que esta água adicional pode fazer no nosso sistema.
Se é uma planta que pretende vender energia apenas às custas de contrapressão (cogeração pura), o eventual consumo adicional de vapor no processo não seria nenhum empecilho para o difusor, desde que haja bagaço disponível.
Se é uma planta que tem matriz de produção com até 1,5 s/tc (grande produção de álcool), a evaporação desta água adicional também pode ser gerenciada sem muita dificuldade, pois parte do caldo pode ser desviado diretamente para a produção de álcool.
Por outro lado, se a matriz de produção está dedicada para o açúcar em sistema de três massas, com produção de álcool apenas do mel residual bem esgotado, toda esta água deverá ser evaporada. E se a mesma planta pretende ainda gerar energia também por condensação, o que exige máxima sobra econômica de bagaço, esta água adicional poderá ser um elemento complicador a ser considerado.
Esta última condição é a que merece uma análise mais detalhada, pois é onde haveria maior desvantagem para o difusor.
Considerando-se que os equipamentos de processo sejam os mesmos, uma simulação rápida mostra que o aumento de embebição poderá representar um consumo adicional de cerca de 40 kg/tc. Para a nossa moagem de 500 t/h isto significa 20 t/h de vapor que poderia ser condensado. Se este vapor estivesse sendo usado em uma turbina de condensação com vapor a 64 bar / 450 C com eficiência mínima de 80%, seria possível gerar cerca de 4.600 kW, e vender cerca de 4.100 kW em função da energia parasita (cerca de 10%) inerente aos sistemas de condensação. Vemos que é um número muito próximo daquele encontrado na comparação do vapor motriz, mas a vantagem final estaria com a moenda.
Porém, sempre existe o recurso de investirmos em equipamentos de processo, na evaporação principalmente, visando manter o mesmo consumo específico de vapor de processo, mesmo com maior taxa de embebição. O custo destas instalações adicionais deverá ser comparado com a receita anual adicional proporcionada pelo menor consumo de vapor motriz no difusor.
No momento em que escrevemos temos discutido valores de venda de energia que vão desde R$ 50,00/MW.h para o estado do Paraná, onde existe abundância de energia, até R$ 100,00/MW.h no estado de Goiás, onde há escassez de energia. Tomando um valor médio de R$ 75,00, o faturamento anual adicional com o difusor seria de aproximadamente R$ 900.000,00 para a diferença de potência indicada acima. Trata-se de um valor considerável, o qual muito provavelmente retorna em dois ou três anos, dependendo da capacidade da planta.
Esta comparação nos leva a recomendar o difusor se levarmos em conta apenas os aspectos da cogeração de energia. Naturalmente deverão ser levados em conta os aspectos relativos aos custos de implantação dos dois sistemas, as diferenças na extração e na manutenção, etc.
Após estas considerações, muito provavelmente a vantagem continuaria com o difusor, no caso da instalação de uma nova planta de extração de caldo, principalmente porque o vapor que não passaria pelas turbinas a vapor da moenda poderia ser gerado a maior pressão a aumentar ainda mais a vantagem em favor da difusão.