A Manutenção Durante o Projeto
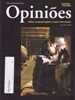
Felizmente estamos em época de vacas gordas, inclusive com perspectiva de duração mais prolongada que de costume. Como conseqüência, muitas novas unidades industriais estão sendo projetadas e implantadas.
A exemplo do que ocorre com as usinas eficientes já em operação, as novas unidades deverão ser projetadas para apresentar custos operacionais cada vez menores. Desta maneira, caso sobrevenha uma época de vacas mais magras e preços mais baixos, as novas plantas terão condições de continuar produzindo açúcar e álcool com os menores custos do mundo.
Dentre os custos operacionais de uma usina, a manutenção tem uma importância relevante. Assim, desenvolver o projeto industrial pensando em mínimos custos de manutenção é uma condição indispensável.
Neste sentido, um princípio importante deve ser obedecido: “Para uma dada capacidade, menos equipamentos de maior porte geram menores custos de manutenção do que mais equipamentos de menor porte”. Maior número de equipamentos significa mais tubulações, mais válvulas, mais instrumentos, mais isolamento térmico, mais acionamentos, etc. Tudo isto aumenta o custo de manutenção.
Por outro lado, para adotar o princípio acima é importante ter em mente o aspecto da modularidade dos equipamentos e das instalações. É preciso definir com boa precisão o horizonte de produção de cana ao longo dos anos, para em seguida definir os módulos industriais daí decorrentes.
O estudo da modularidade permite escolher as capacidades típicas dos equipamentos principais seguindo receitas mais ou menos padronizadas. Por exemplo, duas caldeiras para cada linha de moendas. Dois aparelhos de destilação para cada caldeira, e assim por diante.
O uso de equipamentos de grande porte pressupõe esquecer aquele velho ditado que tem feito parte da cultura do nosso setor: “Quem tem dois tem um, quem tem um não tem nenhum”. É preciso ter apenas um equipamento com adequada confiabilidade. Os primeiros jatos transcontinentais foram desenhados com quatro turbinas, o que garantia aos projetistas máxima segurança durante as travessias sobre os oceanos. Ao longo dos anos a confiabilidades das turbinas foi aumentando e, em conseqüência, há hoje inúmeros jatos cruzando oceanos com apenas dois motores.
A confiabilidade dos equipamentos depende fundamentalmente do projeto e da manutenção. Com relação à manutenção, as usinas têm o privilégio de dispor de quatro a cinco meses por ano para as atividades de manutenção. Tempo é o que não falta. Há inúmeras outras atividades industriais que devem rodar durante todo o ano e desenvolver as atividades de manutenção em tempo muito mais reduzido. Não há desculpas para se iniciar uma safra com manutenção mal feita por falta de tempo.
Resta assim tratar de instalar equipamentos que tenham projetos com elevada confiabilidade e com reduzidas necessidades de manutenção.
A confiabilidade tem dois aspectos principais: capacidade (nominal e efetiva) e disponibilidade de tempo de operação sem falhas.
Os equipamentos devem ser desenhados com suficiente folga para que a sua capacidade nominal seja realmente a sua capacidade efetiva. Lembramos de outro antigo “dogma” do nosso setor: “Operar caldeiras novas no máximo com 90% da sua capacidade”. É um absurdo. Você imagina a Embraer vendendo um jato de 100 lugares e recomendando ao cliente para embarcar somente 90 passageiros? Cláusulas contratuais específicas devem ser negociadas visando garantia de operação contínua dos equipamentos na capacidade nominal durante o mínimo de 5.000 horas por safra e com garantia de disponibilidade mínima de 98% do tempo.
A disponibilidade depende naturalmente do projeto dos equipamentos, mas depende também dos materiais adotados. Os equipamentos na usina são submetidos de forma constante a processos de deterioração causados por abrasão e/ou por corrosão. A escolha de materiais mais nobres, resistentes à abrasão e à corrosão, certamente vai reduzir muito o número de paradas e os custos de manutenção. É portanto indispensável fazer uma avaliação entre o maior custo inicial destes materiais e a economia resultante nos anos vindouros. A tendência é que as plantas do futuro serão cada vez mais “inoxidáveis” do que as atuais. A tendência é também operar cada vez mais com cana sem lavar, o que vai exigir mais materiais anti-abrasão.
As bombas da usina merecem um capítulo à parte. A tendência é a instalação de apenas uma bomba no campo, ficando as bombas reserva no almoxarifado para emergências. As bombas devem ser especificadas com o mesmo critério de confiabilidade acima exposto, ou seja, selecionadas com folga de forma a poder operar com conversor de freqüência, com materiais adequados para resistir à corrosão / abrasão e sem risco de cavitação. Com estes cuidados a bomba deve operar 5.000 horas sem problemas, e muita tubulação e válvulas podem ser economizadas.
As novas plantas estão sendo projetadas com a maior parte dos equipamentos ao tempo. Há muito poucos edifícios. Esta realidade exige o desenho de pipe racks para a condução das tubulações diversas. Os pipe racks devem ser desenhados de forma generosa, de maneira a possibilitar as ampliações que certamente virão e a facilitar os trabalhos de manutenção. Os pipe racks devem também estar desenhados para servir de condução de cabos elétricos e de comando, seja por via aérea, seja por via subterrânea.
Com os equipamentos ao tempo, o acesso para a manutenção em áreas elevadas deve ser feito por guindastes automotores. A planta portanto deve ser desenhada em blocos ou quarteirões, que permitam o fácil acesso destes veículos por todos os lados.
Em resumo, é sempre importante considerar que decisões inadequadas durante o projeto podem resultar em maiores custos de manutenção durante toda a vida útil da usina.