Clássico X Moderno
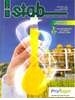
Tive uma viagem de trabalho à França na semana que antecedeu a data de entrega deste texto.
Desta vez o avião pousou no Terminal 2 (T2) do aeroporto Charles de Gaulle (CDG) em Roissy. Fazia muito tempo que eu não passava pelo T2, pois quando a TAM passou a fazer parte da Star Alliance os seus aviões passaram a usar o T1.
Conheci o T1 do aeroporto CDG bem na época da VARIG, início dos anos 90. Fiquei maravilhado com a ousadia inovadora do projeto daquele terminal. Tudo era revolucionário para mim. O edifício das partidas e chegadas é o “sol” de um sistema com vários edifícios “planetas” em volta onde os aviões estacionam. Do “sol” para os “planetas” existem túneis para os passageiros acessarem os aviões. Nos túneis existem esteiras subterrâneas pelas quais os passageiros são transportados. Na época tudo muito inovador e surpreendente.
Com o aumento da demanda o aeroporto CDG teve que ser ampliado e o T2 foi implantado. Para a minha decepção o projeto de ampliação nada tinha a ver com a filosofia que fora adotada no T1. O arranjo físico do T2 era digamos muito mais “clássico” do que o arranjo físico “moderno” do T1.
Nesta viagem pude verificar que o T2 já recebeu uma grande obra de expansão da sua capacidade. Claro que eu não sou especialista em projetos aeroportuários, mas dá para intuir que arranjo físico do projeto do T1 seria muito mais complicado para ser ampliado. Seria esta a causa da mudança de paradigma dos projetos? Foram os projetistas forçados a voltar do “moderno” para o “clássico”?
Esta situação nos faz lembrar o conhecido ditado: “Clássico é o moderno que não sai de moda”.
Mas comecei com toda esta introdução para discutirmos uma situação similar que estamos vivendo em nossa atividade profissional. Trata-se de certos arranjos físicos ”modernos” que os fabricantes estão propondo para turbinas a vapor de contrapressão e de condensação para acionamento de geradores elétricos com potência de 40 MW a 60 MW.
Temos estudado detalhadamente desde 2006 os prós e os contras dos diversos arranjos possíveis, e estamos convencidos de que a melhor solução é a instalação destas máquinas em paralelo, em bases com aproximadamente 5 m de altura, condensador sob as turbinas de condensação e em edifícios com pontes rolantes para manutenção. Esta é a solução que foi adotada em projetos “greenfield” de grupos com tradição no setor agroindustrial, como a Usina Santa Adélia e a Usina São Martinho. A solução com 9 m de altura só faz sentido nos casos em que o espaço horizontal disponível na indústria é muito escasso, obrigando-nos a aumentar a altura do edifício para poder alojar equipamentos elétricos diversos. Trata-se dos arranjos que poderíamos chamar de “clássicos”.
Recentemente temos visto os fabricantes de turbinas tradicionais proporem alternativas “modernas” para a instalação dos turbo geradores (TG) de grande potência, entre elas:
- Alternativa 1: TG de contrapressão montado no piso zero (A1);
- Alternativa 2: TG de contrapressão com carenagem metálica ao tempo com manutenção por guindaste (A2);
- Alternativa 3: TG de condensação com condensador lateral, conhecido como “telefone” (A3);
- Alternativa 4: TG de condensação com condensador traseiro, conhecido como “axial” (A4);
- Alternativa 5: TG de condensação com condensador evaporativo.
Todas as alternativas acima têm em comum o apelo de ser “moderno” e de procurar reduzir o investimento nas obras civis do edifício da CGT e das bases dos equipamentos. Mas tudo tem seu preço e a economia líquida tem que levar em conta vários outros aspectos.
A A1 naturalmente reduz custo das obras civis, porém todas as tubulações de vapor motriz, extrações controladas, tomadas para aquecimento e vapor de escape tem que chegar à turbina por cima da máquina. Hoje em dia os clientes exigem que os projetos das tubulações atendam à norma NEMA SM 23, o que significa tubulações muito flexíveis e bem suportadas e guiadas. Temos assim que instalar estruturas metálicas robustas dentro do edifício para suportar as cargas horizontais. Estas estruturas e tubulações sobre as turbinas dificultam demais o acesso para manutenção, sendo que no nosso setor o procedimento de sopragem das linhas deve ser anual. Não há espaço para o tanque de óleo sob a turbina, a menos que se use uma base metálica muito reforçada como tanque de óleo, mas o risco de vibrações seria considerável em máquinas de grande capacidade. Se o tanque fica na lateral da máquina muito mais espaço horizontal é necessário, pois hoje em dia é inadmissível projetarmos a instalação sem respeitarmos a Norma NR-12 que determina acessos e passagens livres. A drenagem de condensados fica mais difícil exigindo uma série de canaletas. Estas máquinas acima de 40 MW com tanque metálico incorporado estão pelo menos a 1,5 m do nível zero, exigindo assim um piso metálico falso sobre o nível zero para garantir acessibilidade para manutenção.
A A2 visa eliminar o edifício e a ponte rolante, montando o TG dentro de uma carenagem metálica termo acústica desmontável e utilizando guindaste automotor para montagem e manutenção. Em nossa opinião esta é uma solução que pode ser válida apenas para condições específicas. A CGT deve estar próxima de centros que disponham de guindastes na faixa de 250 a 400 t, pois o custo de mobilização de uma máquina destas é muito elevado. É válida também para uma instalação com apenas um TG. No caso das usinas de açúcar temos geralmente 3 TG’s que não são montados simultaneamente, e neste caso três mobilizações do guindaste para regiões remotas custam mais do que uma ponte rolante. A carenagem adequada também é cara em função das suas características especiais, e esta alternativa naturalmente deve vencer as dificuldades que foram listadas na A1. O acesso para manutenção fica complicado pela necessidade de desmontagem da carenagem, além de já termos os tubos chegando por cima da turbina.
A A3 com “telefone” parece muito conveniente no papel até que surge a necessidade de você instalar uma turbina destas. Como o nível de vácuo no condensador afeta o desempenho da turbina, a perda de carga no “telefone” deve ser a mínima possível com vapor de alto volume específico. Para potências altas estes tubos têm entre 2,5 e 3,0 m de diâmetro. Devem ser instalados com suportes de mola especiais, pois embora o vapor tenha temperatura baixa em operação normal, nas partidas o estudo de flexibilidade deve considerar temperaturas na faixa de 85 ºC. Tubos com estas dimensões sobre a turbina para serem desmontados com a ponte rolante acabam exigindo edifícios tão ou mais altos do que uma turbina de mesma potência instalada a 5,0 m de altura com condensador inferior.
A A4 com condensador “axial” também pode ser interessante quando existe apenas um TG. Ou então quando vamos instalar no máximo dois em um arranjo “back to back” em linha, com cada condensador nos extremos opostos da instalação. Instalar duas máquinas deste tipo em paralelo fica difícil porque os condensadores vão naturalmente aumentar a distância mínima necessária entre as máquinas e vão criar dificuldades para a passagem das tubulações de vapor. E é importante lembrar que neste tipo de máquina um dos mancais do eixo somente pode ser acessado para manutenção através de uma abertura no tubo entre a turbina e o condensador, obrigando a necessidade de soluções especiais de engenharia para garantir a acessibilidade.
A A5 com condensador evaporativo traz complicações novas e relevantes para projetarmos o tubo de vapor sob vácuo atendendo integralmente a norma NEMA SM 23. As tubulações têm diâmetros muito grandes e, ao contrário do condensador “axial” que pode se movimentar sobre sapatas especiais quando ocorre a dilatação no tubo, um enorme condensador evaporativo, que evidentemente não se move, exige a instalação de juntas de dilatação muito especiais. É uma instalação cara e complicada.
Resumo da ópera. Nossas experiências recentes têm demonstrado que na ânsia de reduzir custos de obras civis foram criados outros tipos de problemas de instalação e de manutenção. Em nossa opinião a economia não compensa.
Para nós continua imbatível o “clássico” arranjo de turbo geradores em paralelo montados a 5.0 m de altura, com condensador inferior e um pequeno fosso para instalar a bomba de condensado e o sistema de vácuo do condensador. Ninguém gosta de fossos abaixo do piso zero em usinas, mas um fosso dentro de um edifício limpo e pressurizado, convenhamos, é muito melhor do que um monte de tubos sobre uma turbina.
Somos os maiores incentivadores de inovações tecnológicas. Em particular nesta visita à França estive visitando uma empresa que tem a sua “Sala da Inovação”. Ali semanalmente quem quiser pode participar de reuniões que discutem novas ideias de maneira informal e sem considerar níveis hierárquicos. Uma excelente iniciativa!
Mas toda inovação deve ser bem avaliada. Soluções que são muito adequadas para outros setores da indústria podem eventualmente não ser as mais adequadas para a nossa agroindústria.