A Lei do Perea
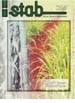
Iniciei este texto no mesmo dia em que foram anunciadas as medidas de racionamento de energia elétrica no Brasil, quando reunimos a família para determinar como seria possível economizar pelo menos 20% de energia elétrica.
Toda crise tem o seu lado positivo. É interessante verificar o número de hábitos “irracionais” que adotamos em casa e no escritório no que diz respeito ao consumo de energia elétrica, sendo que muitos deles podem ser corrigidos sem necessariamente abdicarmos do conforto que a energia proporciona.
Tive o privilégio na vida de poder trabalhar com técnicos muito competentes, entre eles o eng. Luiz Perea na Usina da Barra. Quando estávamos projetando juntos novas instalações, o Luiz sempre dizia brincando: “Cuidado, em uma usina de açúcar o número de motores ligados é sempre igual ao número de motores instalados”. A equipe batizou esta frase como “A Lei do Perea”, e em função dela todos estávamos sempre atentos com o aumento de carga elétrica nos projetos. Era uma época de abundância.
Desde aquela época a postura nas usinas tem mudado muito, e hoje em dia os técnicos dão uma maior importância ao consumo específico de energia elétrica (kw.h/tc). Naturalmente, quanto menor for este consumo, maior será o excedente exportável de energia elétrica para a rede da concessionária.
Por outro lado, novas técnicas às vezes exigem instalação de motores elétricos, como por exemplo circuladores mecânicos para tachos operando com vapor de aquecimento a baixa temperatura, evaporadores de película de filme descendente, bombas de vácuo para condensadores barométricos, etc. Quando instalamos estes motores temos que nos preocupar em instalar a menor potência possível, e ao mesmo tempo procurar economizar em outro lugar para não aumentar o fator kw.h/tc, e se possível procurar até diminuí-lo.
Procuramos listar a seguir alguns critérios que podem ser úteis na redução daquele fator.
Em primeiro lugar é preciso verificar se os motores já em operação estão trabalhando com um bom fator de potência, ou seja, com amperagem o mais próxima possível da nominal sem correr risco de desligar. Registradores de corrente são muito úteis e devem fazer parte do arsenal para avaliar o comportamento durante um certo período de tempo. Motores com potência exagerada devem ser trocados. Sistemas que exigem variação de carga ou de rotação devem contar preferencialmente com conversores de freqüência, sempre que possível.
Descontando-se a energia mecânica consumida na preparação e na moagem da cana, a maior parte da energia mecânica consumida na usina é utilizada no bombeamento de fluídos, sejam líquidos ou gases. Para se ter uma planta eficiente do ponto de vista global, a maior parte desta energia deveria vir preferencialmente de motores elétricos, e portanto é nestes motores que devemos focar a nossa possibilidade de economia em primeiro lugar.
Os equipamentos de bombeamento (bombas, ventiladores, exaustores, etc) devem estar projetados para operar com boa eficiência, 75% no mínimo e se possível acima de 80%. Esta é uma tarefa para profissionais. O tempo de fabricar bombas ou exaustores na usina já passou. É preciso especificar junto com o fabricante e depois medir a eficiência durante a operação para exigir os resultados prometidos. Uma curva de bomba de fabricante idôneo, um manômetro e um amperímetro fornecem dados valiosos para o engenheiro de campo.
Por outro lado é freqüente encontrarmos bons equipamentos operando fora do seu ponto ideal de performance, o que acarreta desperdício de energia. Os equipamentos devem ser bem projetados, mas também devem ser bem especificados e selecionados.
A energia consumida é proporcional à massa de fluído deslocada e ao diferencial de pressão.
O diferencial de pressão depende em grande parte do processo, mas também da perda de carga nas linhas. Os equipamentos, dutos, tubulações e seus acessórios devem ser projetados com perdas de carga razoáveis e admissíveis. Há que fazer um balanço entre investimento inicial e energia consumida. Com os preços da energia subindo, maiores investimentos quase sempre se pagam rapidamente. Devemos tolerar pressões elevadas no processo somente quando os equipamentos assim o exigirem, sem alternativas. Processos que utilizam dispositivos tipo venturi, transporte pneumático, ou similares, devem, na medida do possível, ser substituídos por serem ineficientes do ponto de vista energético. Trocadores de calor devem ser dimensionados segundo esta visão. E assim por diante.
Falando agora das massas deslocadas, temos pouca margem de manobra em relação ao caldo extraído e aos produtos dele conseqüentes. O que podemos fazer é procurar trabalhar sempre com o mínimo possível de recirculações no processo. Conforme já discutimos aqui antes, a fábrica deve ser o mais “curta” possível.
Para bombear menor volume de gases temos que procurar operar as caldeiras com o menor excesso de ar possível, o que aliás é indispensável para uma boa eficiência de queima do bagaço. É interessante enfatizar como a adoção de processos mais eficientes sistematicamente implica em menor consumo líquido de energia mecânica. Com relação ao volume de ar necessário para o secador de açúcar, não há muito que possamos fazer. Ventiladores de torres de resfriamento devem ser dotados de conversores de freqüência para se adequarem às condições climáticas ao longo do dia. E assim por diante.
Mas sistemas de bombeamento de água são os grandes vilões consumidores de energia mecânica na usina. É aí que podemos atuar para ter grandes ganhos absolutos de energia. Podemos dividi-los em captação, lavagem de cana, produção de álcool e produção de açúcar.
A distância da captação é função da condição física de cada usina e o que podemos fazer é procurar reduzir ao mínimo o volume necessário de água. Necessidades específicas de irrigação da cana devem ser consideradas e levadas em conta.
Sistemas de lavagem de cana podem e devem ser eliminados procurando-se trazer cana o mais limpa possível e procurando-se adaptar o processo para operar com as impurezas que inevitavelmente vão acompanhar o caldo de cana não lavada.
Na produção de álcool devemos usar sempre que possível sistemas em série, ou seja, usar a mesma água de resfriamento da fermentação, que não deve estar acima de 31 a 32 C, para o resfriamento dos condensadores dos aparelhos de destilação. Esta última pode voltar por gravidade para o sistema de resfriamento. O consumo de água nos condensadores é proporcional ao consumo de vapor de aquecimento das colunas de destilação. Usamos menos vapor com um teor alcoólico mais alto no vinho. Usamos menos vapor quando operamos as colunas com uma menor taxa de refluxo dos condensadores, o que significa que aparelhos bem projetados e bem operados vão consumir menos vapor e portanto menos água. Condensadores bem projetados, que permitem a operação com um maior diferencial de temperatura da água, também vão ajudar muito.
Na produção de açúcar podemos atuar em duas frentes. Em primeiro lugar, procurando reduzir a massa de vapor a ser condensada. Em segundo lugar, usando equipamentos que permitam condensar esta massa de vapor com o menor contingente possível de água de resfriamento.
Na evaporação podemos reduzir a massa de vapor do ultimo efeito aumentando as sangrias nos diversos efeitos. Mais sangria significa menor consumo de vapor e portanto menor consumo de água, algo análogo ao que discutimos na destilação.
No cozimento podemos reduzir a massa de vapor a ser condensada evitando a recirculação desnecessária e a conseqüente diluição excessiva dos méis. Em resumo, quanto menor a quantidade de água adicionada ao processo, menor será a quantidade de vapor a ser condensado, e portanto menor a necessidade de água de resfriamento.
A utilização de condensadores barometricos representa uma expressiva redução de consumo de energia mecânica. A potência adicional representada pelas bombas de vácuo é amplamente compensada pela redução do volume de água bombeada para um ambiente que está sob vácuo, ao contrario dos condensadores tipo multijato de necessitam de pressão para operar. Hoje em dia estamos reduzindo ainda mais a potência das bombas de vácuo, pela instalação de uma única bomba de partida para todos os tachos. Esta bomba de partida entra em operação apenas para a formação do vazio, sendo desligada em seguida. Desta maneira as bombas de vácuo que operam durante o cozimento podem ser muito menores.
Após discutir o bombeamento dos fluídos, temos os transportadores de sólidos, cana, bagaço e açúcar principalmente. Temos que usar arranjos físicos que permitam menores distâncias de transporte e, na medida do possível, privilegiar transportadores do tipo correia no lugar de transportadores de arraste e de roscas helicoidais.
Centrífugas para levedura e para açúcar são outros consumidores representativos de energia mecânica.
Na fermentação a maior arma é operar com o maior teor alcóolico possível, diminuindo os volumes. Na centrifugação de massa A existe a possibilidade de recuperação de energia durante a frenagem, mas esta técnica exige uma bateria de centrifugas idênticas onde se privilegia a recuperação de energia em detrimento da capacidade de produção. O preço da energia no futuro vai dizer se é uma solução, além de técnica, economicamente viável. Outra possibilidade será a adoção de centrifugas continuas, sempre que o processo o permitir.
E de uma forma geral, para revogarmos a “Lei do Perea”, é indispensável conscientização e treinamento. Não custa repetir que plantas eficientes consomem menos energia. Usina que opera de forma regular, parando pouco e de forma planejada, tem um menor fator kw.h/tc.
Que tal aproveitarmos a crise e adotar a meta de tentar baixar o nosso fator em 20%? Seria mais ou menos como passar de cerca de 15 kw.h/tc para 13 kw.h/tc. É muita energia!