Utilidades
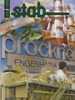
As usinas e destilarias tem equipamentos e instalações que geralmente são divididos em processo e utilidades. As assim chamadas utilidades mais importantes são vapor, água, energia elétrica e ar comprimido, sendo esta a sua ordem de importância na indústria.
De uma forma geral, as utilidades servem para fornecer e retirar energia do processo, para transferir energia de um ponto a outro ou para transformar a energia em suas mais diferentes formas de aplicação. Mas sempre que definirmos, as utilidades de uma usina, de uma certa forma estamos definindo a eficiência energética daquela planta.
É interessante constatar que maior consumo vapor acarreta maior consumo de água. Por sua vez, maior consumo de água acarreta maior consumo de energia elétrica. Ar comprimido não tem relação direta com vapor e água, apenas com a energia elétrica. Vamos procurar discutir alguns aspectos desta constatação.
O vapor é a mais importante das utilidades, pois não operamos sem ele. Podemos até considerar a hipótese, absurda de comprar energia elétrica da concessionária e de trabalhar por algum tempo sem captação de água, mas sem vapor não tem negócio.
Toda a energia necessária no processo, seja na forma de energia mecânica ou na forma de energia térmica, provem da queima do bagaço e é distribuída na usina por meio do vapor. Portanto, menor consumo de vapor significa menor consumo de energia por tonelada de cana processada. E energia excedente, hoje em dia, cada vez vai ter maior valor no mercado.
Dissemos acima que maior consumo de vapor representa maior consumo de água. Podemos comprovar esta afirmativa com vários exemplos.
Talvez o exemplo mais evidente possa ser uma destilaria de álcool anidro com ciclo hexano. Se consideramos o conjunto da destilaria como sendo uma caixa de entradas e de saídas de energia, temos entrando a energia contida no vinho e no vapor. Temos saindo a energia contida nas perdas no isolamento térmico (normalmente pequenas), a energia contida no álcool anidro (pequena porque o álcool é cerca de 9% do vinho e já sai resfriado), a energia contida no condensado do refervedor "L", a energia contida na vinhaça e a energia retirada pela água de resfriamento. A energia contida na vinhaça é representativa e corresponde a cerca de 50% da energia contida no vapor. Mas praticamente a outra metade da energia é retirada do sistema através da água de resfriamento, cuja necessidade aumenta com o aumento do consumo específico de vapor do aparelho. Portanto, aparelhos que consomem mais vapor exigem mais água de resfriamento.
Outro exemplo típico está na evaporação. Para reduzir o consumo de vapor no processo temos que fazer sangrias de vapor nos primeiros três efeitos. Sempre que fazemos isto, reduzimos a quantidade de vapor produzida no último efeito, o qual vai para o condensador. Menor quantidade de vapor no condensador significa menor quantidade de água de resfriamento.
Como na usina, sem contar os equipamentos de preparação de cana e de extração do caldo, os maiores consumidores de energia mecânica são as bombas de água e os ventiladores das caldeiras, um menor consumo de água vai certamente representar um menor consumo de energia elétrica.
Das utilidades acima mencionadas, a energia elétrica é aquela que pode ser vendida mais facilmente no mercado. Se considerarmos um preço de venda de R$ 100,00 / MW.h e uma safra de 4.000 horas efetivas, uma economia na potência consumida na usina de um kW pode representar um faturamento adicional de R$ 400,00. Se desligamos um motor de 100 CV podemos receber cerca de R$ 30.000,00 adicionais no final da safra.
Desta maneira, na instalação de novos equipamentos é sempre importante avaliar a potência instalada e consumida nos motores elétricos correspondentes. Via de regra, equipamentos mais baratos consomem mais energia elétrica.
Um caso típico são os trocadores de calor a placas. Os coeficientes de troca térmica são maiores quanto maiores forem as velocidades dos fluidos dentro do trocador, mas serão maiores também as perdas de carga e portanto a potência consumida nas bombas. É prudente desconfiar sempre de trocadores muito baratos. É preciso estudar uma solução de compromisso entre a potência consumida e o preço do trocador.
Caldeiras para geração de vapor são outro caso a estudar com cuidado. Além de exigir uma boa eficiência no sentido de recuperar todo o calor contido nos gases de combustão, é importante sempre avaliar o consumo de energia mecânica por tonelada de vapor produzido. Em casos recentes, encontramos diferenças de até 1.000 CV instalados em caldeiras de 250 t/h de capacidade.
Por outro lado, a produção do açúcar e do álcool continua sendo a razão de ser da empresa, e portanto não podemos deixar de instalar potência às custas de redução da eficiência industrial. O importante é ter sempre em mente a necessidade de avaliar se a energia instalada vale mais ou menos do que o ganho de eficiência esperado.
Se instalamos um agitador em uma dorna ou em um pré fermentador, é preciso avaliar se o ganho de eficiência esperado é maior do que o valor de venda daquela energia, e depois procurar comprovar na prática.
Se instalamos uma bomba adicional de massa cozida com alto brix, para poder alimentar as centrífugas de forma satisfatória, é preciso verificar se a potência na bomba é compensada pela maior produtividade das centrífugas. E assim por diante.
Falamos anteriormente sobre maior consumo de água, o que vale também para os sistemas de captação e de tratamento de efluentes. Quanto menor for a captação e menor a quantidade de efluentes, melhor.
Uma cana típica tem cerca de 70% de água, ou seja, 700 kg/tc. Com 26% de bagaço e bagaço com 50% de umidade, 130 kg/tc vão para atmosfera nos gases de combustão ou para o estoque de bagaço excedente. Com 30% de embebição e aproveitando condensados resfriados com o caldo misto para esta finalidade, usamos 300 kg/tc, sobrando portanto 270 kg/tc, ou 27% da cana.
Temos que procurar adequar a nossa instalação para usar estes 27% em todas as necessidades de água do processo, como lavagem de telas de filtros, diluição de produtos, limpeza de equipamentos, etc. Se conseguirmos este intento, vão restar apenas as necessidades de água de reposição da caldeira e de água de reposição nos sistemas de resfriamento.
Uma usina típica consumindo 45% de vapor (450 kg/tc) e produzindo 1,5 saco/tc, vai usar aproximadamente 260 kg/tc de água de reposição nos sistemas de resfriamento. Naturalmente este valor depende de condições específicas de cada projeto, conforme discutimos acima. Considerando uma reposição máxima de 20% nas caldeiras, vai usar cerca de 90 kg/tc. Temos portanto um consumo de teórico de 350 kg/tc, o qual deveria ser o objetivo dos projetos futuros de novas usinas. Como já existem usinas com consumo de água na faixa de 500 kg/tc, trata-se de um objetivo perfeitamente factível, o qual vai significar uma grande economia de energia elétrica, pois menor captação de água vai representar menor produção de efluentes.
E para terminar sobre as utilidades é interessante mencionar a famosa rede geral de ar comprimido, tão comum em muitas usinas, na qual cada setor instala consumidores sem muito critério. O consumidor mais indesejável são os sistemas de jato de areia, com consumo muito elevado. É importante separar adequadamente a rede de ar de instrumentação da rede de ar de serviço, pois são consumos muito diferentes de ar comprimido com qualidades também muito diferentes. Um sistema de pressostatos deve garantir sempre a preferência para a rede de instrumentação, pois a rede de ar de serviço pode ter os seus consumidores devidamente classificados pela sua ordem de importância no processo, evitando assim picos de consumo que acarretam picos de energia elétrica.
Discorremos assim sobre as utilidades de uma usina. Na próxima vez, vamos procurar falar sobre algumas "inutilidades" que ainda existem em nossas usinas. Se você lembra de alguma inutilidade em particular, escreva relatando.