O Tamanho da Caldeira
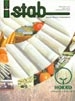
Recebemos uma consulta de um cliente potencial perguntando se trabalhamos com sistemas de cogeração. Respondemos que todo técnico açucareiro que se preza trabalha com cogeração. As usinas de açúcar e de álcool são plantas que se encaixam perfeitamente no conceito de plantas propícias para a cogeração de energia elétrica.
Plantas industriais em geral consomem energia na forma de energia mecânica (acionamentos diversos) e na forma de energia térmica (trocadores de calor). Uma planta industrial é tanto mais adequada para a implantação de sistemas de cogeração quanto menor for a relação entre a energia mecânica (EM) e a energia térmica (ET) utilizadas.
Numa usina de açúcar e álcool usamos tipicamente 15 kW.h/tc no preparo e na moagem e mais 15 kW.h/tc nos motores elétricos diversos. Se admitirmos, por exemplo, um consumo de vapor no processo de 50,0% (500 kg/tc), isto corresponde a uma energia de aproximadamente 300 kW.h/tc. Chegamos assim a uma relação EM / ET de 15+15 / 300 = 0,1, o qual é um valor muito baixo quando comparado com outras plantas industriais diversas. Portanto, a cogeração é uma vocação natural para as usinas de açúcar, e mais ainda porque o nosso combustível, o bagaço, tem um preço muito competitivo. Naturalmente esta relação varia muito de caso para caso, mas o que importa aqui é a ordem de grandeza da relação, que é sempre baixa nas usinas.
Tanto é assim que as usinas podem facilmente atingir a sua auto suficiência em energia sem grandes dificuldades técnicas. Basta termos vapor a pelo menos 21 bar e turbinas medianamente eficientes para atingir este objetivo.
Entretanto, se pretendemos exportar energia elétrica, as alternativas técnicas que de abrem são inúmeras. Queremos aproveitar esta oportunidade para discutir alguns conceitos sobre como definir a capacidade das caldeiras aplicadas em sistemas de cogeração.
A capacidade de geração de vapor deve ser definida inicialmente em toneladas por safra. É preciso determinar o volume disponível de bagaço por safra, o qual vai depender do contingente de cana processado e das características desta cana (fibra, tipo de colheita, etc). Depois é preciso determinar a eventual existência de combustíveis auxiliares, provenientes de biomassa ou não.
Uma vez determinada a quantidade de bagaço produzida por safra, é preciso considerar um estoque de segurança de bagaço. Esta folga, que varia desde 4,0% até 7,0%, é importante para garantir o combustível necessário durante as partidas e as paradas da usina. Esta margem tem que ser tanto maior quanto menor for a eficiência de aproveitamento de tempo na indústria, pois quanto mais paradas houver, mais bagaço se consome. Safras longas, sujeitas portanto a maiores períodos de chuva, também recomendam estoque de segurança mais generoso.
É preciso agora determinar quanto vapor se produz com uma tonelada de bagaço. Dependemos fundamentalmente do poder calorífico inferior (PCI) do bagaço, da pressão / temperatura do vapor gerado, da temperatura do condensado e da eficiência da caldeira.
O PCI do bagaço está relacionado com vários fatores, mas a sua umidade é a variável mais preponderante e em cujo valor podemos influir mais diretamente. Apenas para mencionar um caso estudado recentemente, um bagaço cuja umidade passou de 51,3% para 50,0% representou um acréscimo de 3,5% na produção de vapor, o que significa muito dinheiro.
A energia necessária para gerar o vapor será a diferença de entalpia entre o condensado e o vapor. Quanto maior a pressão do vapor, maior esta diferença. Devemos também lembrar que o condensado proveniente do vapor de escape pode retornar para a caldeira com cerca de 120 C, mas o condensado de turbinas de condensação retorna com temperatura na faixa de 50 C. Portanto, neste último caso é necessário prever sangrias nas turbinas a vapor para fazer o pré aquecimento do condensado, o que significa consumo adicional de bagaço.
Por último é preciso adotar uma eficiência ao PCI da (s) nova (s) caldeira (s). Caldeiras modernas com eficiência ao PCI de 87,0% já são uma realidade. Projetos mais recentes pretendem atingir até 89,0 / 90,0% de eficiência, mas então começam as dificuldades decorrentes de se obter gases de chaminé com temperaturas muito baixas, de até 130 C, que provocam condensação e a conseqüente corrosão nos equipamentos. Há novas técnicas sendo desenvolvidas para contornar estes problemas, e temos certeza de que se o preço da energia valer a pena, soluções de engenharia serão encontradas.
Mas se adotamos uma eficiência de 87,0%, com todos os outros parâmetros estabelecidos será possível determinar a massa de vapor produzida por safra. Conhecendo as horas efetivas de safra, chegamos à produção potencial média horária de vapor em uma safra.
A questão então é definir com quantas caldeiras vamos produzir este vapor: com uma, com duas ou com três? Se for mais de uma, seriam iguais ou não? A resposta passa pela definição de uma série de critérios de projeto.
Do ponto de vista de menor investimento inicial, apenas uma caldeira seria a resposta natural. Caldeiras de até 350 t/h já estão disponíveis, a atenderiam uma usina processando cerca de 3.000.000 t de cana. Inconvenientes possíveis seriam a maior dificuldade de operação em cargas baixas e a menor confiabilidade da planta como um todo.
Do ponto de vista de confiabilidade operacional, duas caldeiras com alguma folga de projeto poderiam permitir a continuidade da moagem na eventual falta de uma delas, mesmo que com capacidade reduzida. Mas seria uma solução de maior investimento inicial.
Do ponto de vista de operação na entressafra, é imprescindível dispor de uma caldeira de capacidade relativamente pequena, pois não é possível dispor de contingentes de bagaço excedente comparáveis com os volumes queimados durante o período de safra. Desta maneira, se for economicamente interessante vender energia na entressafra, será fundamental dispor de uma caldeira que possa operar com menor capacidade sem perder eficiência. Quando falamos em entressafra, vale lembrar que uma parada por chuva durante três dias é uma espécie de mini entressafra. Se temos turbinas de condensação e temos caldeiras adequadas para continuar gerando vapor com menor capacidade, esta é uma grande vantagem competitiva. Com este enfoque, três caldeiras seriam uma solução técnica perfeita, embora mais custosa em investimento e em manutenção.
Os critérios acima nos induzem a verificar cuidadosamente a especificação técnica de uma caldeira nova no que diz respeito à sua flexibilidade operacional, que os especialistas chamam de "turn down" (operação com capacidade reduzida). Os fabricantes falam em "turn down" de até 1:4, ou seja, operar com até 25% da capacidade nominal, mas informam que abaixo de 65% da capacidade nominal a eficiência começa a cair muito rapidamente. Para que isto não ocorra o projeto da caldeira deve ser muito especial e complicado, o que acaba nos levando para a adoção de mais de uma caldeira.
Podemos exemplificar os critérios acima com um caso prático de um projeto de cogeração de uma usina processando 2.500.000 t de cana. Verificamos que a massa de bagaço disponível permitiria gerar 350 t/h de vapor a 65 bar, sendo que neste caso específico a geração na entressafra é altamente recomendável com combustível auxiliar, o que significa dispor de turbinas de condensação com condensador de 100 t/h.
Estudamos quatro possibilidades de capacidades de caldeiras:
- 350 t/h
- 175 t/h + 175 t/h
- 200 t/h + 150 t/h
- 250 t/h + 100 t/h
A alternativa adotada foi a de duas caldeiras de 175 t/h. O cliente optou por uma maior confiabilidade operacional, pois se uma caldeira sair de linha a usina foi planejada para operar com cerca de 60% de capacidade de moagem e com alguma redução de consumo no processo. Na entressafra, a operação com cerca de 63,0% da capacidade permite adequar o projeto para operação ainda com eficiência satisfatória. Partidas e paradas ficam mais fáceis, e os equipamentos ficam todos padronizados. Não é a mais barata, mas não deixa de ser uma boa solução.
Mas cada caso é um caso. Todas as particularidades da nova planta devem ser cuidadosamente avaliadas para chegarmos a uma solução com boa relação custo / benefício.