A Temperatura do Vapor
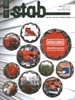
Inúmeras vezes, discutindo com clientes a respeito de novas instalações para cogeração de energia elétrica, aparecia na discussão a premissa de que não seria conveniente ter a temperatura do vapor nas turbinas acima de 480 ºC.
Sempre que tentávamos explicar que com uma temperatura de 520 ºC poderia haver ganhos na cogeração, a resposta era sempre a mesma: o custo da instalação com 520 ºC seria muito mais elevado e no final das contas não haveria ganho significativo, porque o vapor de escape sairia mais quente das turbinas.
Não adiantava tentar argumentar. A temperatura de 480 ºC acabou tornando-se uma espécie de paradigma para o mercado. Era mais ou menos proibido ultrapassá-la.
Vamos procurar discutir estas duas considerações. A primeira diz respeito ao custo da instalação.
Procuramos estudar um caso típico e prático de uma caldeira produzindo 200 t/h de vapor a 67 bar abs. numa usina planejada para ser eletrificada, já que para uma planta nova de cogeração caldeiras menores não fazem muito sentido econômico.
Ao passarmos o vapor desta caldeira de 480 ºC para 520 ºC, teremos acréscimos de custo inicial basicamente nos seguintes componentes: na caldeira propriamente dita, na tubulação de vapor vivo até a casa de força, nas válvulas de bloqueio de vapor vivo, na estação redutora de vapor de 67 bar e na turbina a vapor do gerador.
O custo inicial de uma caldeira de 200 t/h a 67 bar / 480 ºC gira ao redor de R$ 25 milhões, e a sua montagem ao redor de R$ 3 milhões. Para a temperatura de 520 ºC o valor da caldeira passa para R$ 26 milhões, e não há diferenças no custo da montagem, fundações, etc. Temos portanto uma diferença em torno de R$ 1 milhão.
O peso da tubulação de vapor vivo até a casa de força, neste exemplo prático, foi estimado em 38.000 kg de tubos com material em ASTM A335 P11 para a temperatura de 480 ºC. Para a temperatura de 520 ºC o peso foi estimado em 45.000 kg com material ASTM A335 P22. A diferença total de preço entre as duas soluções foi orçada em cerca de R$ 375 mil.
É importante ressalvar que o código ASME permite a utilização de materiais do tipo T22 e P22 (fabricados no Brasil) até o limite de temperatura de 520 ºC, desde que as espessuras e os critérios de cálculo obedeçam às normas aplicáveis. Temos inclusive um documento com parecer técnico de empresa certificadora confirmando esta possibilidade.
As válvulas de bloqueio de vapor vivo, para o mesmo exemplo prático acima, passam da classe 900 para a classe 1500 quando aumentamos a temperatura do vapor de 480 ºC para 520 ºC. Orçamos o custo inicial deste conjunto de válvulas para os dois casos, e chegamos a uma diferença total de R$ 70 mil, lembrando que em usinas eletrificadas há relativamente poucas válvulas para vapor motriz.
Um fabricante da estação redutora de vapor, com válvulas do tipo que já faz a saturação do vapor na própria válvula, informou que não há diferença de preço entre as temperaturas de 480 ºC e 520 ºC.
Os fabricantes de turbinas a vapor também informaram que não há diferenças de preços significativas entre as duas temperaturas. O gerador também não muda de preço, bem como a subestação para conexão com a concessionária e outros equipamentos elétricos correlatos.
Somando todas as diferenças de valor acima consideradas, chegamos a um total aproximado de R$ 1,45 milhões. Para gerar vapor a 520 ºC em vez de 480 ºC, gastamos cerca de 2% a mais de bagaço. Porém, as turbinas a vapor bem dimensionadas vão ter um consumo médio aproximadamente 5% menor. Devemos obter portanto um ganho líquido da ordem de 3% de energia gerada.
Ocorre que o vapor de escape vai apresentar temperaturas distintas para máquinas com eficiência termodinâmica similar: mais ou menos 150 ºC e 170 ºC respectivamente para o vapor vivo com temperatura mais baixa e mais alta. Para baixarmos estas temperaturas do vapor de escape até 135 ºC, vamos necessitar vazões diferentes de água no desuperaquecedor: 14,1 kg/t e 33,0 kg/t nos dois casos acima.
Como há um consumo de água 130% maior no segundo caso e considerando que o consumo de vapor no processo seria constante, o vapor vivo na admissão da turbina seria aproximadamente 2% menor ((33,0 – 14,1)/1000), diminuindo assim a energia gerada.
Mas em nossa opinião trata-se de um falso dilema.
Se o sistema de cogeração contempla turbinas de condensação, o problema não existe, pois todo o bagaço será usado e a totalidade de vapor vivo passará por alguma turbina de qualquer maneira, seja nas de contrapressão, seja nas de condensação.
Se o sistema de cogeração contempla apenas turbinas de contrapressão, temos então um doce problema: como aumentar o consumo de vapor de processo em cerca de 2% ? Podemos dar várias sugestões. A primeira delas é aumentar a embebição. Não temos evaporação suficiente? Podemos reduzir um pouco as sangrias. E assim por diante. Normalmente é difícil reduzir o consumo de vapor de processo. Aumentar é a coisa mais fácil. O último recurso que podemos lançar mão é a condensação atmosférica, ou seja, ferver água residual e lançar o vapor na atmosfera.
Mas voltando ao nosso exemplo de uma caldeira de 200 t/h e 480 ºC em uma usina eletrificada, verificamos que para uma safra de 1.500.000 t de cana seria possível exportar cerca de 96.000 MW.h, considerando 40% de consumo de vapor sobre a cana no processo e o restante com turbina de condensação.
Quando passamos a temperatura desta caldeira para 520 ºC aumentamos a energia exportada para cerca de 2.800 MW.h por safra. Admitindo um valor de venda de R$ 125 / MW.h, temos um faturamento adicional por safra de R$ 350.000,00 e o retorno da diferença de investimento em cerca de cinco safras. Como estamos tratando de equipamentos com uma vida útil mínima de 30 anos, teríamos cerca de 25 anos para usufruir de aproximadamente 3% a mais de energia sem custo adicional.
Com os valores de energia elétrica que foram praticados no último leilão, vale sempre a pena fazer contas antes de decidir pela temperatura de 480 ºC.
Queremos agradecer à eng. Cristiana Crepaldi, que com sua paciência determinou com precisão os pesos e os Reais acima mencionados.