A Recuperação do Condensado de Escape
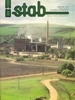
Todos sabemos que na indústria temos dois tipos de caldeira para geração de vapor. As caldeiras propriamente ditas, as quais a partir do bagaço geram o vapor vivo cuja maior parte é usada nas turbinas, e as “caldeiras do processo”, as quais a partir do vapor de escape das turbinas geram o vapor vegetal que é utilizado para várias finalidades, tais como aquecimento, evaporação, cozimento, destilação, etc.
As “caldeiras do processo” são os pré-evaporadores, e as usinas que têm pré-evaporadores com superfície de troca térmica adequada para condensar todo o vapor de escape que é produzido nas turbinas já deram um enorme passo para a otimização do seu balanço térmico.
Poder condensar todo o vapor de escape nos pré-evaporadores significa também poder dispor de uma grande fonte de água quente de excelente qualidade para a alimentação das caldeiras, reduzindo a um mínimo indispensável a necessidade de água de reposição.
Entretanto, além da excelente qualidade do condensado de escape como água propriamente dita, que pode ser avaliada em sólidos dissolvidos, dureza, etc., é importante preservar a “qualidade energética” deste condensado, que via de regra está na faixa de 125 C dependendo da pressão do vapor de escape.
É assim muito importante procurar retornar o condensado do escape (CE) diretamente ao desaerador, sem permitir que o CE baixe de temperatura pelo efeito de flash quando o mesmo é enviado a tanques atmosféricos. A energia que se perde deixando o CE baixar, por exemplo, de 125 a 95 C pode ficar entre 4 a 5% da energia necessária para se gerar o vapor correspondente a 20 bar/300 C.
O retorno do condensado para o desaerador pode ser feito através de purgadores ou de bombas. Teoricamente é também possível utilizar um sifão, mas na prática, devido às pressões de vapor de escape na faixa de 2,5 bar, seriam necessárias colunas de equilíbrio muito grandes que dificultam esta solução.
A utilização de purgadores é possível quando a soma da pressão interna do desaerador (normalmente na faixa de 1,2 bar), mais o desnível geométrico entre o fundo da calandra do evaporador e o topo do corpo horizontal do desaerador, mais a perda de carga no purgador e mais a perda de carga na linha, é menor do que a pressão interna do evaporador (normalmente na faixa de 2,5 bar). Entretanto, alguns cuidados devem ser tomados, a saber:
- é preciso considerar o caso mais crítico, vapor de escape com pressão mínima e desaerador na pressão normal;
- é preciso dimensionar corretamente os purgadores, determinando claramente a pressão diferencial à qual serão submetidos, pressão esta que determina a capacidade de remoção de condensado; é importante checar a seleção com o fabricante correspondente;
- é preciso lembrar que após o purgador existe fluxo bifásico (mistura de líquido e vapor) devido ao efeito de flash parcial, e isto deve ser levado em conta na avaliação da perda de carga;
- é importante ter de preferência linhas independentes para cada purgador, para que não haja interferência entre os mesmos e para que se possa monitorar, por meio de visores, a operação de cada um;
- é preciso lembrar que em certas circunstâncias pode haver uma coluna de líquido a jusante do purgador sem que haja uma coluna de líquido a montante do mesmo;
- é recomendável o uso de purgadores de bóia de alta capacidade com os acessórios correspondentes (filtro, visor, etc.).
Quando o uso de purgadores não é possível ou recomendável, é necessária a utilização de bombas centrífugas. Mesmo quando há desnível suficiente, a solução por meio de bombas tem a vantagem de substituir vários purgadores no caso de a usina possuir vários evaporadores.
A utilização de bombas exige a instalação de um tanque de CE, de preferência horizontal, cuja elevação do seu topo fique logo abaixo da elevação da parte inferior das calandras dos evaporadores. Este tanque deve ter a sua pressão equilibrada com a pressão da calandra, por meio de um tubo que liga as partes superiores dos dois equipamentos. Para se garantir que não vai haver passagem de vapor para este tanque, é necessária a instalação uma pequena coluna de equilíbrio que vai compensar possíveis variações de pressão no sistema.
O nível no tanque de CE é mantido constante por meio de uma válvula de controle, a qual se instala a jusante da bomba. Esta válvula garante que não haverá cavitação da bomba por falta de líquido e ao mesmo tempo garante que não haverá fuga de vapor de escape do sistema. Trata-se de um sistema simples e confiável.
Esta solução exige parte dos mesmos cuidados que já foram mencionados anteriormente, e além destes, os seguintes:
- o tanque de CE deve ser previsto para a pressão de vapor de escape;
- o tanque de CE deve estar o mais alto possível, para aumentar o NPSH disponível;
- a bomba deve ser cuidadosamente selecionada, principalmente no que diz respeito ao NPSH requerido/disponível, e deve ter previsto um sistema de água de resfriamento de gaxetas ou eventualmente selo mecânico;
- o tubo de retorno de condensado pode ser único, mas deve ter condição de vencer a soma das vazões de pico do sistema.
A utilização de desaerador é a nosso ver indispensável, mas caso a indústria não disponha deste equipamento, os comentários aqui enunciados prevalecem para o retorno de CE para a caixa de água quente que alimenta a caldeira. Neste caso continuamos a aproveitar uma parte da energia contida no CE.
As figuras seguintes ilustram de forma esquemática as duas soluções descritas anteriormente.