A Desidratação de Álcool por Peneira Molecular
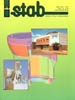
A maior parte das usinas e destilarias brasileiras está no momento pensando na solução de duas questões: a substituição do benzol por ciclo-hexano ou outro agente desidratante e o aumento de capacidade de produção de álcool anidro.
Nesta hora cabe pensar em uma alternativa de processo que é a utilização de peneira molecular, pois dependendo das condições de cada usina ou destilaria esta é uma possibilidade que pode ser técnica e economicamente interessante.
Pretendemos neste artigo fazer uma descrição sucinta do processo com suas vantagens e desvantagens, e em seguida listar as situações em que a peneira pode ser uma alternativa vantajosa.
O processo por peneira molecular utiliza como elemento desidratante substâncias minerais chamadas zeólitos (estruturas cristalinas de alumínio-silicatos), os quais são conhecidos pelo homem desde há muito tempo. Existe uma grande gama de zeólitos naturais e uma classificação específica dos mesmos segundo a configuração da sua estrutura cristalina.
Os zeólitos passaram a ter utilização industrial, principalmente na indústria petroquímica, a partir de 1962. Hoje em dia os zeólitos comerciais são substâncias sintéticas produzidas por várias empresas.
No caso da desidratação do etanol, são utilizados zeólitos sintéticos de estrutura cristalina do tipo A, material este que se apresenta na forma de pequenas esferas, e que por este motivo é às vezes chamado de “resina”, embora o processo em questão não envolva resinas de troca única.
Os zeólitos sintéticos têm a característica de apresentar porosidades cujas dimensões são praticamente constantes. A Figura 1 indica um diagrama no qual aparece a distribuição dos tamanhos de porosidades para três materiais distintos. Este diagrama mostra que as porosidades dos zeólitos estão na faixa de 10 SÍMBOLO 143 \f “MS LineDraw” (SIMBOLO 143 \f “MS LineDraw” =m.10-9), o que significa dimensões na faixa de “moléculas”, o que aliás levou os cientistas a batizar o processo de “peneira molecular”, pois é como se pudéssemos imaginar um “peneiramento” a nível de moléculas.
Os zeólitos têm a capacidade de, sob certas condições de pressão e de temperatura, adsorver maiores ou menores quantidades da água contida no álcool hidratado. A técnica de desidratação consiste, portanto em passar a mistura hidroalcoólica pelo leito de zeólitos, onde a água fica retida e, em seguida, desidratar (ou “regenerar”) o leito de zeólitos e assim sucessiva e alternadamente. Há, portanto a necessidade de se ter sempre dois leitos de zeólitos em operação, um na fase de adsorção e outro na fase de regeneração.
Basicamente existem dois procedimentos para a regeneração dos zeólitos, um denominado TSA (“temperature swing adsorption”) e outro denominado PSA (“pressure swing adsorption”). O procedimento TSA leva em conta que a quantidade de água adsorvida diminui com o aumento da temperatura, para uma dada pressão. O procedimento PSA leva em conta que a quantidade de água adsorvida diminui com a diminuição da pressão, para uma dada temperatura.
O procedimento TSA é adotado nos processos em que a mistura hidroalcoólica é tratada, por exemplo, na fase líquida, sendo que a regeneração dos zeólitos é feita pela passagem de gases quentes através do leito (nitrogênio, gás carbônico, etc., a cerca de 200 C).
O procedimento PSA é adotado nos processos em que a mistura hidroalcoólica é tratada na fase vapor, sendo que a regeneração dos zeólitos é feita pela passagem de parte do álcool anidro produzido através do leito que neste momento está sob vácuo.
Os processos modernos utilizam sempre o procedimento PSA (desidratação na fase vapor), já que evita a necessidade de geração de gases quentes e aumenta a vida do zeólito, pois o mesmo não fica sujeito à fadiga devido à variação constante da temperatura (redução da vida útil devido a choques térmicos).
A Figura 2 mostra um diagrama muito simplificado do processo. O álcool hidratado é vaporizado e superaquecido, passando então pelo leito “A”. A água fica retida e na saída do leito temos álcool anidro na fase vapor que depois é condensado e resfriado. Enquanto isto, parte do álcool anidro produzido passa pelo leito “B” que está neste momento sob vácuo, arrastando consigo a água que ficou retida no ciclo anterior e gerando um álcool fraco com teor alcoólico aproximado de 75 GL. O processo se inverte constantemente, sendo que cada ciclo, dependendo do grau GL do álcool na entrada e da capacidade de adsorção do zeólito, pode durar de 5 a 8 min.
Vamos procurar agora listar as principais características do processo.
- O consumo de vapor é de cerca de 1/3 daquele necessário para a desidratação por ciclo-hexano. São necessários 0,50 kg/l de vapor a baixa pressão (vapor de escape ou mesmo vapor vegetal) e 0,05 kg/l de vapor à pressão de 5 bar abs. (para o superaquecimento do álcool hidratado vaporizado). O consumo total é, portanto de 0,55 kg/l, contra 1,5 a 1,6 kg/l no caso do ciclo-hexano.
- O consumo de água de resfriamento é essencialmente o mesmo quando comparado com o ciclo-hexano, ou seja, cerca de 40 a 45 kg/l, dependendo da temperatura da água fria.
- O consumo de energia elétrica é de cerca de 2 kw.h/l na planta propriamente dita. Há que acrescentar a este valor o consumo de energia necessária para a circulação da água de resfriamento que varia de indústria para indústria.
- O consumo de ar comprimido para os sistemas de controle é de cerca de 2,4 Nm³/l.h.
- O espaço físico necessário para uma planta com capacidade de 300 m³/d é de aproximadamente 8 m x 15 m. A planta fica normalmente ao tempo.
- Como o ciclo adsorção/regeneração é muito curto, o sistema deve necessariamente ser totalmente automático. Não há, portanto a necessidade de operadores adicionais. Um sistema de automação bem projetado e bem instalado é, portanto de capital importância para a boa operação da planta.
- O álcool fraco produzido pode ser retornado a uma coluna retificadora existente, embora neste caso deve-se levar em conta o que isto representa em termos de capacidade desta coluna.
- Outra possibilidade é investir um pouco mais e prover a unidade de peneira molecular com uma pequena coluna retificadora que substitui o evaporador de álcool. Neste caso, sem nenhum consumo adicional de vapor, a unidade fica totalmente independente da necessidade de ser operada simultaneamente com outros aparelhos de destilação.
- A alternativa acima abre o excelente horizonte de permitir a possibilidade de se operar a unidade durante todo o ano, viabilizando muito mais o retorno do capital investido. Evidentemente, há que verificar a disponibilidade de bagaço excedente e a possibilidade de se operar uma pequena caldeira durante a entressafra sem causar transtornos para a manutenção da usina/destilaria.
- O investimento inicial é maior para o sistema de peneira molecular quando comparado com a instalação de uma coluna desidratadora por ciclo-hexano. Entretanto, pode eventualmente não ser, caso o aumento da produção de álcool anidro signifique, por exemplo, a necessidade de se investir em maior geração de vapor. Isto deve ser estudado detalhadamente caso a caso.
- O custo operacional da peneira molecular é mais baixo. Estima-se um custo máximo de reposição do zeólito de R$ 0,65/m³ de álcool produzido contra R$ 0,80/m³ no caso do ciclo-hexano (adotamos consumo de 0,80 kg/m³ e preço de R$ 1,05/kg). Porém, o grande fator de economia pode estar na grande redução do consumo de vapor e na possibilidade de se operar a planta durante todo o ano.
- O processo por peneira molecular não introduz elementos tóxicos ao produto final. Trata-se, portanto de um processo mais adequado caso a usina/destilaria pretenda trabalhar com alcoóis especiais para aplicações mais finas visando principalmente o mercado de exportação.
A simples adaptação de colunas existentes que operam com benzol para passar a operar com ciclo-hexano é evidentemente muito mais barata do que a implantação de um sistema de peneira molecular.
Entretanto, caso a usina/destilaria esteja pensando em adquirir uma nova coluna desidratadora por ciclo-hexano, um estudo mais cuidadoso dos custos/benefícios do sistema de peneira molecular é necessário para que a decisão final seja a mais acertada para cada caso específico.